lower forming forces | high forming degrees
lower forming forces | high forming degrees
Precision parts with tight tolerances | good surface structure
Precision parts with tight tolerances | good surface structure
hot forging & cold forming
The production methods in forming technology are classified on the basis of various criteria. One of these criteria is the temperature of the workpiece, with a distinction being made between forging and cold forming. At Güldner, both of these production methods are used. In the following, we would like to explain the two forming techniques and highlight their respective advantages.
Hot forging
Hot forging refers to all forming processes that are carried out above the recrystallization temperature of a metal. During the forming process, solidification occurs, which is reversed by planned relaxation phases. This leads to a reduction in the dislocation density in the crystal lattice, as a result of which the material remains malleable and high degrees of deformation can be achieved.
- Working temperature above the recrystallization temperature
- High formability of the materials
- Low forming forces
- Little change in strength and elongation at break in the formed material
- Dimensional tolerances and surface quality worse than with cold forming
- Can generate anisotropy
- Does not cause hardening
The hot forging process, forging on forging presses, is used for small to medium quantities and diameters up to M200. The round material, which is used in bar form, must first be cut to length in a preparatory step. The sections are then heated in whole or in part (in gas, oil or induction furnaces) to forging temperature (depending on the material; up to 1250°C) and partially formed in presses. Machining processes (overturning, thread cutting) are then used to finish such screws, whereby the threads are now mainly produced without cutting (thread rolling) on thread rolling machines.
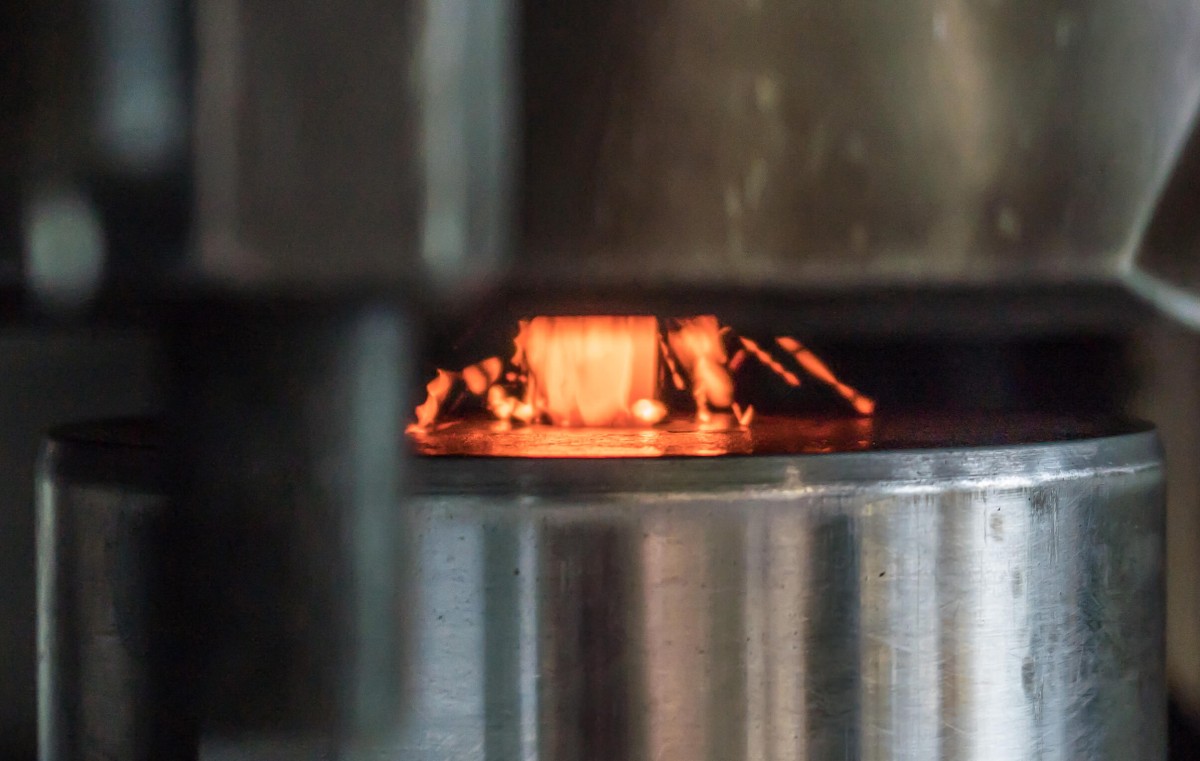
Cold forming
Cold forming is the targeted forming of metals at a temperature significantly below the respective recrystallization temperature. Cold forming refers to uncontrolled plastic deformation (e.g. car accident). Plastic deformation increases the dislocation density in the crystal lattice. As a result, the dislocations in the crystal lattice meet more frequently during their movement and are thus mutually impeded. As a result, greater mechanical work is required for further deformation.
The cold forming process is therefore also noticeable in the mechanical properties of the finished screw or nut. The increase in dislocation density in the crystal lattice increases the tensile strength or yield strength and hardness of the part. This process is generally known as work hardening. The process is used, for example, in the stainless steel sector when screws of strength class A2-70 or A4-70 or A2-80 or A4-80 are to be produced, the strength class of which cannot be increased by heat treatment due to the material properties.
The increased dislocation density leads to stresses in the crystal lattice. One of the consequences of this is that the weldability of the screw or nut cannot be guaranteed. If the screw or nut is brought to the material-specific recrystallization temperature for a sufficiently long time after work hardening, the microstructure relaxes again. However, the recrystallization then also significantly reduces the mechanical properties again. Relatively narrow dimensional tolerances are possible with this process and, in contrast to hot forming, the surface remains without a scale layer.
Cold forming is usually carried out on multi-stage presses and is suitable for large quantities and diameters up to M 30. The starting material is delivered in coils and unrolled and straightened by an upstream straightening machine. Modern cold extrusion presses work in such a way that several operations are carried out one after the other on the machine and the screw leaves the system completely finished. Several operations are carried out in succession with each stroke. (e.g. preforming the hexagon head, upsetting, trimming and reducing the threaded part).
In the subsequent process, the threads are rolled onto the defined threaded parts by thread rolling machines with flat dies or roller and segment tools without cutting. In many cases, presses with integrated thread machining are used. Depending on the diameter and length of the screws, such systems achieve production rates of more than 300 pieces per minute.
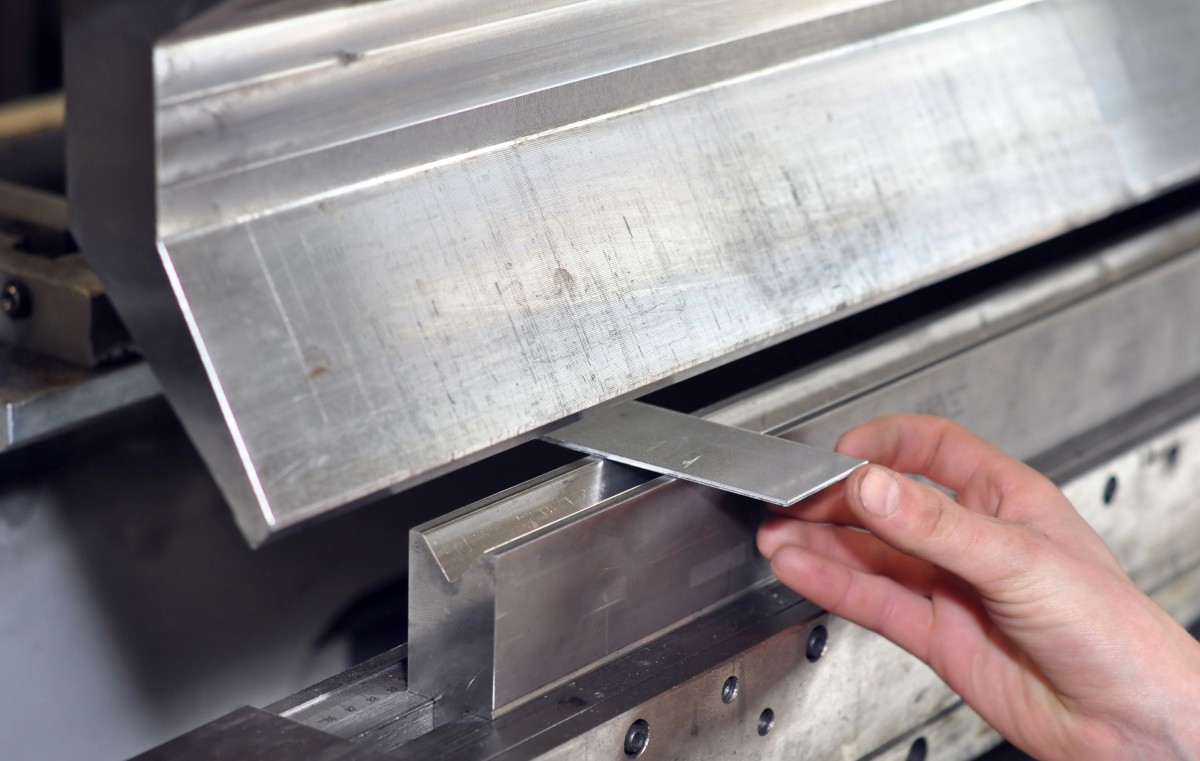
Comparison of hot forging & cold forging forming methods | |
---|---|
Hot forging | Cold forming |
Working temperature above recrystallization temperature | Working temperature lower than recrystallization temperature |
High formability of materials | Precise tolerances |
Low forming forces | No surface scaling |
Strength and elongation at break of the formed material change only slightly | Increase in strength and reduction in ductility, i.e. elongation at break (work hardening) |
Ductile materials can be easily cold formed, for example by processes such as deep drawing, bending or stretching |
Sonderschrauben Güldner GmbH & Co. KG collects and processes the personal data entered in the form in order to process the requested inquiry for you. Please note the marking of the mandatory fields on the forms. The legal basis for this processing of mandatory data is Art. 6 para. 1 lit. b GDPR, implementation of a pre-contractual measure. The processing of the data voluntarily provided by you is carried out on the basis of Art. 6 para. 1 lit. f GDPR. This permits processing that is necessary to safeguard our legitimate interests. Our legitimate interest is to have contact with you, our customers, to improve the quality of our advice and to be able to contact you more easily in the event of any queries. The data collected will only be stored by us for as long as is necessary to process your request and to contact you. It will then be deleted. Translated with DeepL.com (free version)
Additional data protection information, in particular on your rights to information, rectification, erasure, restriction of processing, objection and complaint, can be found in our privacy policy.