Precision + wide product range | Shape and dimensional tolerances for the highest requirements
Precision + wide product range | Shape and dimensional tolerances for the highest requirements
CNC turning and milling - Machining production
The machining production of special screws and nuts using lathes and milling machines is only a marginal area in the production of fasteners compared to forming processes. Nevertheless, this manufacturing process has a right to exist.
In particular, small quantities of drawing parts and special parts can be produced without the need for expensive forming tools. This advantage is particularly important when the fasteners have to be manufactured from special materials designed for the application. The process is also useful when special dimensions or tolerances (deviating from standards) have to be adhered to for special parts such as special screws.
A combination of machining and forming processes is often used in the production of special screws or bolts. For example, the screw blanks (without thread) are produced by machining and then the thread is produced using a cold forming process.
CNC turning
NC turning is a manufacturing process for producing turned parts, especially precision turned parts, using a CNC-controlled lathe. This method makes it possible to achieve complex shapes and tight tolerances.
In CNC turning, a raw material is clamped in a rotating spindle. The workpiece is then machined with various tools to achieve the desired shape and surface. The CNC control makes it possible to precisely control the exact movements and machining steps of the tool.
CNC turning can be used to produce various types of turned parts, such as axles, bushings, special screws, bolts and many other components. The use of CNC-controlled lathes enables high repeatability and precision, which is particularly important when it comes to the production of precision turned parts.
The advantages of CNC turning lie in the efficient production of turned parts in large quantities, the ability to produce complex shapes and geometries, as well as high accuracy and repeatability. CNC turning is used in various industries such as the automotive, aerospace, medical technology, electronics and many other sectors where precision turned parts are required.
In CNC turning, a basic distinction is made between internal and external turning, whereby both types can be carried out by a CNC lathe. The turning process is divided into transverse and longitudinal turning based on the feed direction. Depending on the surface to be machined, there are further subdivisions in turning.
Common process technologies are, for example

Shape turning is often used in the production of precision turned parts where complex shapes and tight tolerances are required. It enables the efficient production of parts with high accuracy and surface quality.
Shape turning uses special tools and tool holders to create the desired shape of the workpiece.
In comparison to conventional turning, where the workpiece is mainly shaped cylindrically, form turning enables the production of complex contours such as grooves, radii, surfaces or even threads. This is achieved by using special tools with different geometries and cutting edges.
The CNC control makes it possible to precisely control the movements of the tool and turn the desired shapes into the workpiece. Various parameters, such as the cutting speed, feed rate and infeed, can be adjusted to achieve optimum results.
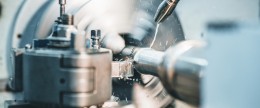
Facing is often used to machine surfaces such as end faces, flat surfaces, offsets or to deburr edges. It can also be used to create specific contours or shapes by programming the tool accordingly.
Facing is a basic CNC turning technique in which the tool is moved at right angles to the axis of rotation of the workpiece. As a result, the outside of the workpiece is machined to create a flat surface or form a specific contour.
In face turning, the workpiece is clamped in the collet or on the chuck of the CNC lathe. The tool then moves along a straight line that runs perpendicular to the axis of rotation of the workpiece. This movement makes it possible to remove material from the surface of the workpiece and create a flat surface.
The advantages of facing lie in its ease of use, efficient material removal and the ability to create precise surfaces and contours. It is used in various industries, such as the automotive industry, mechanical engineering, metalworking and many other areas where precise machining of surfaces is required.
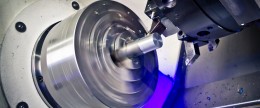
Compared to conventional turning, generating turning enables higher productivity and surface quality. It is particularly suitable for the production of turned parts with a rotationally symmetrical shape such as shafts, bolts, axles and tubes.
In generating turning, the tool is moved along the axis of rotation of the workpiece, while the workpiece itself performs a rotating movement. The tool presses against the workpiece to create the desired shape.
In gear hobbing, a special gear hobbing lathe or a CNC lathe is used, which has a corresponding control. The control system enables precise movement of the tool along the axis of rotation and control of the cutting speed, feed and infeed.
Hob turning offers several advantages, including higher productivity, improved surface finish, longer tool life and increased dimensional accuracy. It is used in various industries, such as the automotive, mechanical engineering and aerospace industries.
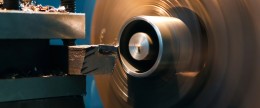
Rotary turning is a basic technique in which the workpiece is machined on a CNC lathe to produce turned parts with cylindrical shapes.
During rotary turning, the workpiece is fixed in the collet or chuck of the CNC lathe. The tool then moves along the axis of rotation of the workpiece to remove material and form the desired cylindrical shape. This method is used to produce cylindrical parts such as shafts, bolts, axles and others.
Rotary turning enables precise machining of workpieces with a high surface quality. The CNC control allows precise control of tool movements and accurate machining. In addition, various tools and cutting tools can be used to form different contours, threads or other features.
Rotary turning is used in numerous industries, including automotive, mechanical engineering, aerospace and many others where cylindrical parts are required.
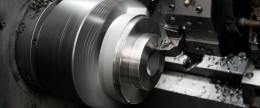
Profile turning uses special tools with different cutting edges and profiles to form desired shapes and contours. These tools can be used in the CNC lathe and allow the machining of complex shapes such as grooves, radii, edges, threads and other contours.
With profile turning, the tool is moved along the axis of rotation of the workpiece to create the desired contours.
The CNC control makes it possible to precisely control the movements of the tool and turn the desired contours in the workpiece. Parameters such as cutting speed, feed rate and infeed can be adjusted to achieve optimum results.
Profile turning is often used in the production of complex turned parts where specific contours and shapes are required. It is used in various industries such as automotive, aerospace, mechanical engineering, medical technology and many others.

This manufacturing process is often used to produce threads on screws, bolts and other components.
Screw turning in the field of CNC turning refers to the production of threads on a workpiece using a CNC lathe.
In screw turning, a cutting tool is used to cut spiral grooves into the workpiece to create a thread.
By using a CNC lathe, complex thread geometries can be produced with high precision.
Multi-spindle turning for medium to large series production of precision turned parts
Multi-spindle turning is a CNC turning process in which several spindles are used simultaneously to perform several machining operations on one workpiece. In contrast to conventional single-spindle turning, in which only one spindle is used to turn the workpiece, multi-spindle turning enables several workpieces to be machined at the same time.
Different machining processes such as turning, drilling, thread cutting or milling can be carried out simultaneously. This allows several workpieces to be machined in a single pass, which leads to a significant increase in productivity.
CNC multi-spindle turning is often used in series production where large quantities need to be manufactured. It enables efficient and cost-effective machining of workpieces, as several machining steps can be carried out in one pass.
Advantages of multi-spindle turning
- Increased productivity – By using multiple spindles, several machining operations can be carried out simultaneously. This significantly reduces the machining time per turned part, resulting in higher productivity.
- Cost savings – By machining several turned parts simultaneously in one pass, costs for machine run times, tool changes and set-up times can be saved. This results in lower production costs per turned part.
- High precision – Multi-spindle turning enables precise machining of turned parts, as the various machining steps are carried out in a single process. This minimizes possible errors or inaccuracies.
- Flexibility – Multi-spindle lathes offer the option of combining different machining steps and tools. This allows complex turned parts with different machining operations to be produced in a single pass.
Precision turned parts for medium to large series production
When you view and play embedded videos on www.gueldner.com, the provider (YouTube) may be able to store your access and analyze your behavior. If you activate the content, i.e. agree to view and play it, a cookie is placed on your computer to record that you have agreed to this in your browser. This cookie does not store any personal data.
For more information, please see our privacy policy and cookie page.
You can also use this link to access the video directly on the plattform of the provider: https://youtu.be/SY0MnQdo-Mg
CNC milling
CNC milling is a process for the precise machining of metal workpieces to produce milled parts. CNC milling uses a computer-controlled milling tool that removes the workpiece step by step to create the desired shape.
The use of CNC milling machines offers numerous advantages in the production of milled parts. On the one hand, the computerized control enables high precision and repeat accuracy, which leads to exact results. In addition, precision milled parts with complex shapes can be produced with a high degree of accuracy.
Another advantage of CNC milling is its efficiency. As the process is automated, large quantities of workpieces can be processed in a short time. This leads to increased production speed and a reduction in costs.
CNC milling is used in the production of prototypes, individual parts, small batches and also in mass production for a wide range of industries such as mechanical engineering, automotive and medical technology.
There are also different types of CNC milling depending on the geometry of the tool. Some of the most important manufacturing processes are, for example
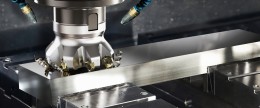
Face milling is preferably used for precise flat surfaces. The finish makes milled parts shine!
CNC face milling is a process in which the milling tool is placed in a perpendicular position to the workpiece. The tool is usually placed face down on the workpiece. Once engaged, the cutter tip abrades the surface of the workpiece, removing some of the material.
There are different types of face milling operations for precision milled parts, including standard face milling and heavy duty face milling.
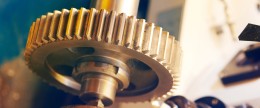
Gear hobbing, a sub-area of milling, is a manufacturing process used for the pre-machining and finishing of gear teeth.
Gear hobbing is one of the continuous gear cutting processes and is characterized by its flexibility and high productivity. The rotary movement of the cutter generates the actual cutting movement. Hobbing can be used to produce all numbers of teeth, profile offsets and helix angles.
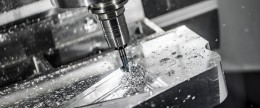
Screw milling is used to produce helical structures. These include threads, spindles and cylindrical screws in particular.
A single-profile thread milling cutter is used for screw milling long threads. The feed rate corresponds to the thread pitch. The tool axis is slightly inclined to the thread axis, which is reminiscent of thread turning.
A multi-profile tool that is aligned parallel to the thread is used for screw milling short threads. In this case too, the feed rate corresponds to the thread pitch. However, only slightly more than one full rotation of the workpiece is required to produce the thread. This process is similar to thread chasing.
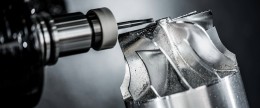
Profile milling can be used to produce milled parts that have shaping elements such as radii and bevels.
Profile milling uses profile cutters that contain the negative of the shape to be produced to create different profiles such as T-slots, dovetail grooves or chip grooves on large milling cutters. Circumferential grooves can also be produced on rotating workpieces. Depending on the type of feed movement, round, straight or any shape can be produced. As many form elements on workpieces, such as radii and bevels, are standardized, there are also correspondingly standardized profile cutters.
There are three types of profile milling: longitudinal profile milling is carried out with a straight feed movement, round profile milling with a circular feed movement and form profile milling with any feed movement.
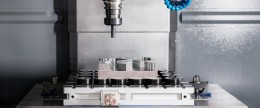
Shape milling is particularly suitable for three-dimensional milled parts.
Shape milling uses tools that do not contain the shape that is to be created. A variety of three-dimensional shapes can be created by controlling the feed movement.
In addition to free-form milling, there is also postform milling, also known as copy milling. These milling processes have become less common since the introduction of CNC control.
Kinematic form milling uses gears, such as cam disks or barrel cams, to generate motion. This method used to be used to produce large series of identical workpieces, but is now rare.
NC form milling uses a numerical control, often in the form of a CNC control. In addition to the three movements in each axis direction, the tools can also be swiveled around two axes to create complex shapes. This process is used for the production of dies in mold making, for the production of casting molds or for turbine blades.

Plunge milling enables the production of milled parts with complex shapes and contours, as the tool can plunge at different angles and depths.
Plunge milling is a milling process in which the milling tool plunges directly into the workpiece to remove material. In contrast to face milling, in which the workpiece is already positioned before the milling process, plunge milling involves plunging the tool into the workpiece.
Plunge milling is often used when processing deep pockets or cavities where the tool cannot penetrate the material from the side.
The advantages of plunge milling include the ability to machine deep holes or pockets, the precision in shaping and the efficiency in material removal. However, due to the plunging process, plunge milling requires careful programming and tool selection to ensure safe and precise machining.
Sonderschrauben Güldner GmbH & Co. KG collects and processes the personal data entered in the form in order to process the requested inquiry for you. Please note the marking of the mandatory fields on the forms. The legal basis for this processing of mandatory data is Art. 6 para. 1 lit. b GDPR, implementation of a pre-contractual measure. The processing of the data voluntarily provided by you is carried out on the basis of Art. 6 para. 1 lit. f GDPR. This permits processing that is necessary to safeguard our legitimate interests. Our legitimate interest is to have contact with you, our customers, to improve the quality of our advice and to be able to contact you more easily in the event of any queries. The data collected will only be stored by us for as long as is necessary to process your request and to contact you. It will then be deleted. Translated with DeepL.com (free version)
Additional data protection information, in particular on your rights to information, rectification, erasure, restriction of processing, objection and complaint, can be found in our privacy policy.