Classification and identification of materials
Classification and identification of materials
Material designation
Understanding the material designation and steel designation
Material designation is a systematic and standardized method of identifying the specific properties of a material. This is particularly important in the metals industry, where there are a variety of materials that can differ greatly in composition and properties.
A material designation for steel, for example, provides information about the chemical composition, mechanical properties and often also the heat treatment of the steel. Here is a brief overview of how a material designation is structured:
- Material number: The material number is a four- to six-digit number that is standardized in DIN EN 10027-2. It is unique and enables uniform identification of the material worldwide.
- Material group: The first digits of the material number provide information about the material group. For example, the digits 1.4 stand for stainless steels.
- Chemical composition: The following digits provide information about the chemical composition of the steel. For example, they can indicate the carbon content or the presence of certain alloying elements.
- Condition symbols: Any attached letters can provide information about the heat treatment (e.g. "H" for hardened) or the mechanical properties (e.g. "Q" for quenched and tempered) of the steel.
An example of such a designation is "1.4301". Here the "1" stands for iron-based alloys, the ".4" for stainless steels and the "301" for the specific chemical composition of this steel, in this case a specific type of stainless steel (also known as "stainless steel").
It is important to understand that the material designation only gives an overview of the basic properties of the steel. For more detailed information, such as exact values for tensile strength, elongation or hardness, you should refer to the manufacturer's material data sheet.
Knowing the material designation is an essential tool for engineers, technicians and anyone involved in the selection and processing of steel and other metals. It enables accurate identification of the material and helps to make the best choice for a particular application.
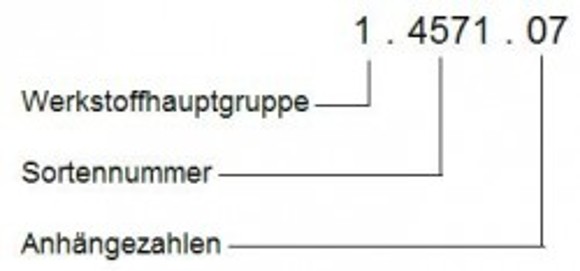
Material and steel designation
A unique designation has been defined for a large number of the materials known today (especially also for ferrous and non-ferrous materials) (cf. DIN EN 10027-2).
Main material groups | |
---|---|
Number | Designation |
0 | Pig iron, ferroalloys, cast iron |
1 | Steel, cast steel |
2 | Heavy metals |
3 | Light metals |
4-8 | Non-metallic materials |
9 | Free |
Sort number | |
---|---|
Digit | Designation |
2 and 3 | Sort class (e.g. chemically resistant steels) |
4 and 5 | Count number |
Steelmaking process | |
---|---|
Digit 6 | Steelmaking process |
0 | indefinite, without meaning |
1 | unquenched Thomas steel |
2 | quenched Thomas steel |
3 | other type of melting - unquenched |
4 | other type of melting - quenched |
5 | unquenched siemens martin steel |
6 | quenched siemens martin steel |
7 | unquenched oxygen inflation steel |
8 | quenched oxygen inflation steel |
9 | Electric steel |
Treatment condition | |
---|---|
Digit 7 | Treatment condition |
0 | None or any treatment |
1 | normalized annealed |
2 | soft annealed |
3 | heat treated for good machinability |
4 | tough tempered |
5 | tempered |
6 | hard tempered |
7 | cold tempered |
8 | feather hard work hardened |
9 | treated according to special specifications |
Source: DIN EN 10027-2 - Designation systems for steels; Part 2: Numbering system |
Material combinations | |||||||||||||||
---|---|---|---|---|---|---|---|---|---|---|---|---|---|---|---|
Nut |
Screw | ||||||||||||||
50 | 70 | KB | YK | YB | KG | GA | GB | GC | V | VH | VW | S | SD | SB | |
50 | O | - | - | - | - | - | - | - | - | - | - | - | - | - | - |
70 | O | O | - | - | - | - | - | - | - | - | - | - | - | - | - |
80 | X | X | - | - | - | - | - | - | - | - | - | - | - | - | - |
KB | - | - | X | - | - | - | - | - | - | - | - | - | - | - | - |
Y | - | - | - | O | O | O | - | - | - | - | - | - | - | - | - |
YK | - | - | - | X | X | X | - | - | - | - | - | - | - | - | - |
YB | - | - | - | O | O | O | - | - | - | - | - | - | - | - | - |
KG | - | - | - | - | - | O | X | - | - | - | - | - | - | - | - |
GA | - | - | - | - | - | X | X | X | X | - | - | - | - | - | - |
GB | - | - | - | - | - | - | O | O | O | - | - | - | - | - | - |
GC | - | - | - | - | - | - | O | O | O | - | - | - | - | - | - |
V | - | - | - | - | - | - | - | - | - | O | O | O | - | - | - |
VH | - | - | - | - | - | - | - | - | - | O | O | O | - | - | - |
VW | - | - | - | - | - | - | - | - | - | O | O | O | - | - | - |
S | - | - | - | - | - | - | - | - | - | - | - | - | O | - | - |
SD | - | - | - | - | - | - | - | - | - | - | - | - | - | O | - |
SB | - | - | - | - | - | - | - | - | - | - | - | - | - | - | O |
X Preferred combination O Permitted combination - Not recommended Source: DIN 267-13 - Mechanical fasteners - Technical delivery conditions - Part 13: Parts for bolted joints with special mechanical properties for use at temperatures from -200 °C to +700 °C |
Seizing of stainless fasteners
The " Seizure " of stainless fasteners between bolt and nut can have different causes:
1. Surface defects in the thread
These are usually caused when rolling threads on already work-hardened surfaces. They are characterized by a cracked, fissured and scaly surface in the thread flanks. These surface defects increase the surface area and thus the attack surface for corrosive influences.
2. Iincorrect tool selection
Under certain circumstances, the tools that are used may not be suitable for processing the material. For example, when cutting a thread, an unsuitable tool may not cut the thread cleanly and completely, resulting in cold welding during assembly. The same applies to the forming of threads. Here, too, the aforementioned situation can occur due to incorrect or defective tools.
3. Hardness difference
One of the most common causes of seizure is a difference in hardness between the screw and nut threads. This difference is essential to prevent the fasteners from permanently bonding ("seizing") through physical-chemical reactions. A hardness difference of at least 50 HV should be aimed for to minimize the risk. As a rule, this is ensured with cold forged fasteners of the same strength class, since the screw thread undergoes significant work hardening in the thread flanks as a result of the forging process. To reduce the risk when using different materials, the delivery states (mechanical properties) of the starting materials should be compared before production.
Additional safety can be achieved by using appropriate sliding pastes, which are applied to the screw thread before assembly. This measure is often used for so-called hot bolted joints to prevent welding of the fasteners at high operating temperatures.
Sources:
Wilke, F. (2002) ThyssenKrupp Steel Kurzbericht 2806 - Wie vermeide ich das Festfressen rostfreier Verbidnungselemente?
Online: http://www.edelstahl-rostfrei.de/downloads/ISER/Festfressen_vermeiden.pdf (05.09.2011)
Duplex steels
General
Duplex steels are materials that have a two-phase structure (ferrite and austenite). Duplex steels are characterized by their combination of properties, which are a mixture of the properties of chromium stainless steels (ferritic or martensitic) and chromium-nickel stainless steels (austenitic).
They have higher strengths than chromium-nickel stainless steels, while exhibiting higher ductility than chromium stainless steels. Their behavior under alternating stresses still exhibits fatigue strength up to an austenite content of about 40%, in contrast to pure austenites. Duplex steels are among the rust- and acid-resistant steels.
PREN-Index
The PREN-Index is a measure of the corrosion resistance of a stainless steel. ASTM G48 specifies the test methods for this.
For corrosion resistant steels, the chemical elements that are critical to corrosion behavior are summarized by the PREN, which establishes a relationship between pitting resistance and chemical composition.
PREN = %Cr + 3.3 x %Mo (ferritic steels)
PREN = %Cr + 3.3 x %Mo + 16 x %N (austenitic steels)
PREN = %Cr + 3.3 x %Mo + 30 x %N (duplex steels)
Ferritic-austenitic duplex steels with PREN > 40 are also known as superduplex steels and are characterized by particularly high corrosion resistance. Steels with PREN values above 32 are considered resistant to salt water.
Sources:
DIN EN ISO 15156-3 - Petroleum and natural gas industries-Materials for use in H2S-containing environments in oil and gas production - Part 3: High alloy steels (CRAs) and other alloys
NACE MR0175/ISO 15156 - Petroleum and natural gas industries-Materials for use in H2S-containing environments in oil and gas production
ASTM G48 - Standard Test Methods for Pitting and Crevice Corrosion Resistance of Stainless Steels and Related Alloys by Use of Ferric Chloride Solution
Strength classes
The strength class for bolts consists of two numbers separated by a point. The number on the left corresponds to 1/100 of the nominal tensile strength Rm in MPa. The number to the right of the dot gives 10 times the ratio between yield strength Re and tensile strength Rm (yield strength ratio). This gives the following values: 0.6 / 0.8 / 0.9. These ratios are multiplied by 10 to give the value after the dot.
Example:
A bolt with tensile strength Rm = 1,000 MPa and a yield strength ratio of 0.9 thus has strength class 10.9.
Formula for determining the strength class
Tensile strength Rm: 1st number X 100
Yield strength Re: (1st number X 100) X (2nd number / 10)
Example:
Screw 10.9
Tensile strength Rm: 10 x 100 = 1,000 MPa
Yield strength Re: (10 x 100) x (9 / 10) = 1,000 x 0.9 = 900 MPa
Overview of old and new strength classes
New designation | 3.6 | 4.6 | 4.8 | 5.6 | 5.8 | 6.6 | 6.8 | 6.9 | 8.8 | 10.9 | 12.9 |
Old designation | 4A | 4D | 4S | 5D | 5S | 6D | 6S | 6G | 8G | 10K | 12K |
Matching nut | 5 | 6 | 8 | 10 | 12 |
Sources:
DIN 267-3 - Mechanical fasteners; Technical delivery conditions; Strength classes for carbon or alloy steel bolts; Conversion of strength classes.
DIN EN ISO 898-1 - Mechanical properties of carbon and alloy steel fasteners - Part 1: Screws with specified strength classes - Standard and fine pitch threads
Weldability of steels
Steels with a carbon content of more than 0.22% are only considered to have limited weldability; additional measures such as preheating are required. However, the carbon content of the steel alone does not provide any information on weldability, as this is also influenced by many other alloying elements. The so-called carbon equivalent (CEV) is therefore taken into account for assessment.
In materials science, the carbon equivalent is a measure for assessing the weldability of unalloyed and low-alloy steels. The carbon content and a variety of other alloying elements in the steel influence its behavior. For the purpose of assessing weldability, the carbon equivalent therefore combines the carbon content and the weighted proportion of elements that influence the weldability of the steel in a similar way to that which would be expected from the carbon into a numerical value. A carbon equivalent value of less than 0.45% implies good weldability. Higher values - depending on the processing thickness - require preheating of the material. Above a value greater than 0.65, the workpiece is only suitable for welding with increased effort, since martensite formation can lead to cold or hardening cracks.
A common procedure for calculating the carbon equivalent value (CEV) is as follows:
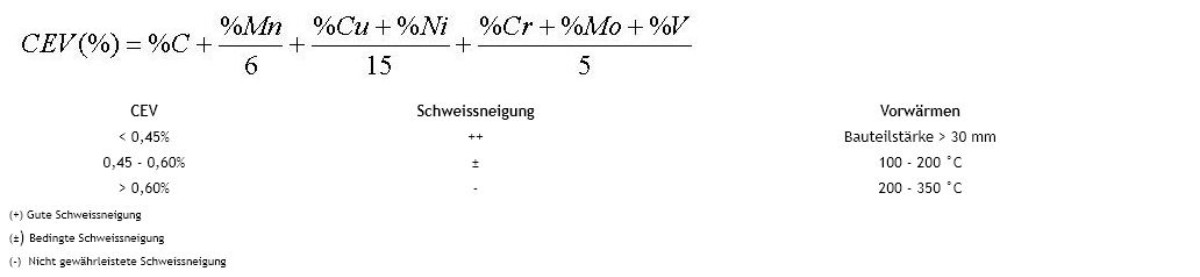
The alloying elements must be entered as a percentage. The carbon equivalent is often given in the material certificate, so that the user does not have to make this calculation himself. However, under certain circumstances, the usability of the CEV given there for the specific application must be questioned.
Source:
Wittel, H. / Muhs, D. / Jannasch, D. / Voßiek, J. (2009) Roloff/Matek Maschinenelemente - Normung, Berechung, Gestaltung; 19th edition; Vieweg+Teubner Verlag; Wiesbaden
ASTM - Materials
Marking | Standard | Description | Material | Comparable EN material |
---|---|---|---|---|
No Grade Mark |
SAE J429 | Bolts, Screws, Studs |
Low or Medium Carbon Steel |
--- |
ASTM A307 Grade A & B |
Low Carbon Steel | --- | ||
SAE J429 Grade 2 |
Low or Medium Carbon Steel |
--- | ||
No Grade Mark | SAE J429 Grade 4 |
Studs | Medium Carbon Cold Drawn Steel |
--- |
B5 | ASTM A193 Grade B5 |
Bolts, Screws, Studs for high temperature service Class 1: Carbide solution treated |
AISI 501 | ~1.7362 |
B6 | ASTM A193 Grade B6 |
AISI 410 | ~1.4006 | |
B7 | ASTM A193 Grade B7 |
AISI 4140, 4142, 4105 | ~1.7225 | |
B16 | ASTM A193 Grade B16 |
CrMoVa Alloy Steel |
~1.7711 | |
B8 |
ASTM A193 Grade B8 Class 1 |
AISI 304 |
~1.4301 |
|
B8C |
ASTM A193 Grade B8C Class 1 |
AISI 347 |
~1.4550 |
|
B8M |
ASTM A193 Grade B8M Class 1 |
AISI 316 |
~1.4401 |
|
B8T |
ASTM A193 Grade B8T Class 1 |
AISI 321 |
~1.4541 |
|
B8 |
ASTM A193 Grade B8 Class 2 |
Bolts, Screws, Studs for high temperature service Class 2: Carbide solution treated and strain hardened |
AISI 304 Strain Hardened |
~1.4301 |
B8C |
ASTM A193 Grade B8C Class 2 |
AISI 347 Strain Hardened |
~1.4550 | |
B8M |
ASTM A193 Grade B8M Class 2 |
AISI 316 Strain Hardened |
~1.4401 | |
B8T |
ASTM A193 Grade B8T Class 2 |
AISI 321 Strain Hardened |
~1.4541 | |
L7 | ASTM A320 Grade L7 |
Bolts, Screws, Studs for low temperature service Quenched and tempered |
AISI 4140, 4142, 4145 |
~1.7225 |
L7A | ASTM A320 Grade L7A |
AISI 4037 | --- | |
L7B | ASTM A320 Grade L7B |
AISI 4137 | ~1.7220 | |
L7C | ASTM A320 Grade L7C |
AISI 8740 | ~1.6546 | |
L43 | ASTM A320 Grade L43 |
AISI 4340 | ~1.6580 | |
B8 |
ASTM A320 Grade B8 Class 1 |
Bolts, Screws, Studs for low temperature service Class 1: Carbide solution treated |
AISI 304 |
~1.4301 |
B8C |
ASTM A320 Grade B8C Class 1 |
AISI 347 |
~1.4550 |
|
B8T |
ASTM A320 Grade B8T Class 1 |
AISI 321 |
~1.4541 |
|
B8F |
ASTM A320 Grade B8F Class 1 |
AISI 303 (Se) |
~1.4305 |
|
B8M |
ASTM A320 Grade B8M Class 1 |
AISI 316 |
~1.4401 |
|
B8 |
ASTM A320 Grade B8 Class 2 |
Bolts, Screws, Studs for low temperature service Class 2: Carbide solution treated and strain hardened |
AISI 304 |
~1.4301 |
B8C |
ASTM A320 Grade B8C Class 2 |
AISI 347 |
~1.4550 |
|
B8T |
ASTM A320 Grade B8T Class 2 |
AISI 321 |
~1.4541 |
|
B8F |
ASTM A320 Grade B8F Class 2 |
AISI 303 (Se) |
~1.4305 |
|
B8M |
ASTM A320 Grade B8M Class 2 |
AISI 316 |
~1.4401 |
|
3 Radial Lines 120° |
SAE J429 Grade 5 |
Bolts, Screws, Studs |
Medium Carbon Steel Quenched and Tempered |
--- |
ASTM A449 | ||||
3 Radial Lines 90° |
SAE J429 Grade 5.1 |
Bolts, Screws, Studs |
Low or Medium Carbon Steel Quenched and Tempered |
--- |
3 Radial Lines 60° |
SAE J429 Grade 5.2 |
Bolts, Screws, Studs |
Low Carbon Martensitic Steel Quenched and Tempered |
--- |
A325 | ASTM A325 Type 1 |
High strength structural bolts |
Medium Carbon Steel Quenched and Tempered |
--- |
--- |
ASTM A325 Type 2 (Withdrawn) |
Low Carbon Martensitic Steel Quenched and Tempered |
--- |
|
A325 |
ASTM A325 Type 3 |
Atmospheric Corrosion Resisting Steel Quenched and Tempered |
--- |
|
BD | ASTM A354 Grade BD |
Bolts, Studs |
Alloy Steel Quenched and Tempered |
--- |
BC | ASTM A354 Grade BC |
--- | ||
5 Radial Lines |
SAE J429 Grade 7 |
Bolts, Screws |
Medium Carbon Alloy Steel Quenched and Tempered |
--- |
6 Radial Lines 60° |
SAE J429 Grade 8 |
Bolts, Screws, Studs |
Medium Carbon Alloy Steel Quenched and Tempered |
--- |
No Grade Mark |
SAE J429 Grade 8.1 |
Studs |
Medium Carbon Alloy or SAE 1041 Modified Elevated Quenched and Tempered |
--- |
A490 | ASTM A490 | High strength structural bolts |
Alloy Steel Quenched and Tempered |
--- |
Sources: http://praticalmaintenance.wordpress.com (24.08.2011) |
Sonderschrauben Güldner GmbH & Co. KG collects and processes the personal data entered in the form in order to process the requested inquiry for you. Please note the marking of the mandatory fields on the forms. The legal basis for this processing of mandatory data is Art. 6 para. 1 lit. b GDPR, implementation of a pre-contractual measure. The processing of the data voluntarily provided by you is carried out on the basis of Art. 6 para. 1 lit. f GDPR. This permits processing that is necessary to safeguard our legitimate interests. Our legitimate interest is to have contact with you, our customers, to improve the quality of our advice and to be able to contact you more easily in the event of any queries. The data collected will only be stored by us for as long as is necessary to process your request and to contact you. It will then be deleted. Translated with DeepL.com (free version)
Additional data protection information, in particular on your rights to information, rectification, erasure, restriction of processing, objection and complaint, can be found in our privacy policy.