Klassifizierung und Identifikation von Werkstoffen
Klassifizierung und Identifikation von Werkstoffen
Werkstoffbezeichnung
Verstehen der Werkstoffbezeichnung und Stahl Bezeichnung
Die Werkstoffbezeichnung ist eine systematische und standardisierte Methode, um die spezifischen Eigenschaften eines Werkstoffs zu identifizieren. Dies ist besonders wichtig in der Metallindustrie, wo es eine Vielzahl von Materialien gibt, die sich in Zusammensetzung und Eigenschaften stark unterscheiden können.
Eine Werkstoffbezeichnung für Stahl, beispielsweise, gibt Auskunft über die chemische Zusammensetzung, die mechanischen Eigenschaften und oft auch über die Wärmebehandlung des Stahls. Hier ist ein kurzer Überblick, wie eine Werkstoffbezeichnung aufgebaut ist:
- Werkstoffnummer: Die Werkstoffnummer ist eine vier- bis sechsstellige Zahl, die in der DIN EN 10027-2 genormt ist. Sie ist eindeutig und ermöglicht eine weltweit einheitliche Identifizierung des Werkstoffs.
- Werkstoffgruppe: Die ersten Ziffern der Werkstoffnummer geben Aufschluss über die Werkstoffgruppe. So stehen beispielsweise die Ziffern 1.4 für nichtrostende Stähle.
- Chemische Zusammensetzung: Die nachfolgenden Ziffern geben Auskunft über die chemische Zusammensetzung des Stahls. Sie können beispielsweise den Kohlenstoffgehalt oder das Vorhandensein bestimmter Legierungselemente anzeigen.
- Zustandssymbole: Eventuell angehängte Buchstaben können Informationen über die Wärmebehandlung (z.B. "H" für gehärtet) oder die mechanischen Eigenschaften (z.B. "Q" für vergütet) des Stahls geben.
Ein Beispiel für eine solche Bezeichnung ist "1.4301". Hier steht die "1" für Eisenbasislegierungen, die ".4" für nichtrostende Stähle und die "301" für die spezifische chemische Zusammensetzung dieses Stahls, in diesem Fall eine bestimmte Art von rostfreiem Stahl (auch bekannt als "Edelstahl").
Es ist wichtig zu verstehen, dass die Werkstoffbezeichnung nur einen Überblick über die grundlegenden Eigenschaften des Stahls gibt. Für detailliertere Informationen, wie z.B. genaue Werte für Zugfestigkeit, Dehnung oder Härte, sollte man auf das Werkstoffdatenblatt des Herstellers zurückgreifen.
Die Kenntnis der Werkstoffbezeichnung ist ein wesentliches Werkzeug für Ingenieure, Techniker und alle, die mit der Auswahl und Verarbeitung von Stahl und anderen Metallen zu tun haben. Es ermöglicht eine genaue Identifizierung des Materials und hilft, die beste Wahl für eine bestimmte Anwendung zu treffen.
Werkstoffbezeichnung und Stahl Bezeichnung
Für eine Vielzahl der heute bekannten Werkstoffe (speziell auch für die Eisen- und Nichteisenwerkstoffe) ist eine eindeutige Bezeichnung festgelegt worden (vgl. DIN EN 10027-2).
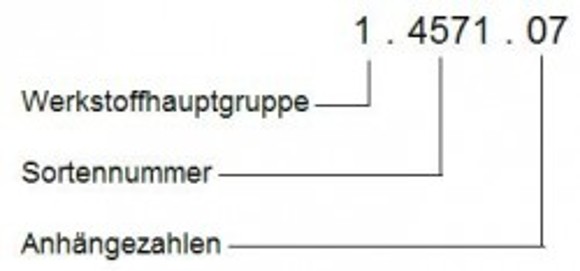
Werkstoffhauptgruppen | |
---|---|
Nummer | Bezeichnung |
0 | Roheisen, Ferrolegierungen, Gusseisen |
1 | Stahl, Stahlguss |
2 | Schwermetalle |
3 | Leichtmetalle |
4-8 | Nichtmetallische Werkstoffe |
9 | Frei |
Sortennummer | |
---|---|
Stelle | Bezeichnung |
2 und 3 | Sortenklasse (z.B. Chemisch beständige Stähle) |
4 und 5 | Zählnummer |
Stahlgewinnungsverfahren | |
---|---|
Stelle 6 | Stahlgewinnungsverfahren |
0 | unbestimmt, ohne Bedeutung |
1 | unberuhigter Thomasstahl |
2 | beruhigter Thomasstahl |
3 | sonstige Erschmelzungsart - unberuhigt |
4 | sonstige Erschmelzungsart - beruhigt |
5 | unberuhigter Siemens-Martin-Stahl |
6 | beruhigter Siemens-Martin-Stahl |
7 | unberuhigter Sauerstoffaufblas-Stahl |
8 | beruhigter Sauerstoffaufblas-Stahl |
9 | Elektrostahl |
Behandlungszustand | |
---|---|
Stelle 7 | Behandlungszustand |
0 | keine oder beliebige Behandlung |
1 | normalgeglüht |
2 | weichgeglüht |
3 | wärmebehandelt auf gute Zerspanbarkeit |
4 | zähvergütet |
5 | vergütet |
6 | hartvergütet |
7 | kaltvergütet |
8 | federhart kaltverfestigt |
9 | behandelt nach besonderen Vorgaben |
Quelle: DIN EN 10027-2 - Bezeichnungssysteme für Stähle; Teil 2: Nummernsystem |
Werkstoffkombinationen | |||||||||||||||
---|---|---|---|---|---|---|---|---|---|---|---|---|---|---|---|
Mutter |
Schraube | ||||||||||||||
50 | 70 | KB | YK | YB | KG | GA | GB | GC | V | VH | VW | S | SD | SB | |
50 | O | - | - | - | - | - | - | - | - | - | - | - | - | - | - |
70 | O | O | - | - | - | - | - | - | - | - | - | - | - | - | - |
80 | X | X | - | - | - | - | - | - | - | - | - | - | - | - | - |
KB | - | - | X | - | - | - | - | - | - | - | - | - | - | - | - |
Y | - | - | - | O | O | O | - | - | - | - | - | - | - | - | - |
YK | - | - | - | X | X | X | - | - | - | - | - | - | - | - | - |
YB | - | - | - | O | O | O | - | - | - | - | - | - | - | - | - |
KG | - | - | - | - | - | O | X | - | - | - | - | - | - | - | - |
GA | - | - | - | - | - | X | X | X | X | - | - | - | - | - | - |
GB | - | - | - | - | - | - | O | O | O | - | - | - | - | - | - |
GC | - | - | - | - | - | - | O | O | O | - | - | - | - | - | - |
V | - | - | - | - | - | - | - | - | - | O | O | O | - | - | - |
VH | - | - | - | - | - | - | - | - | - | O | O | O | - | - | - |
VW | - | - | - | - | - | - | - | - | - | O | O | O | - | - | - |
S | - | - | - | - | - | - | - | - | - | - | - | - | O | - | - |
SD | - | - | - | - | - | - | - | - | - | - | - | - | - | O | - |
SB | - | - | - | - | - | - | - | - | - | - | - | - | - | - | O |
X Vorzugskombination O zulässige Kombination - nicht empfohlen Quelle: DIN 267-13 - Mechanische Verbindungselemente - Technische Lieferbedingungen - Teil 13: Teile für Schraubenverbindungen mit besonderen mechanischen Eigenschaften zum Einsatz bei Temperaturen von -200 °C bis +700 °C |
Festfressen rostfreier Verbindungselemente
Das "Festfressen" von rostfreien Verbindungselementen zwischen Schraube und Mutter kann unterschiedliche Ursachen haben:
1. Oberflächenfehler im Gewinde
Verursacht werden diese in der Regel beim Rollen von Gewinden auf bereits kaltverfestigten Oberflächen. Sie sind gekennzeichnet durch eine angerissene, zerklüftete und schuppige Oberfläche in den Gewindeflanken. Durch diese Oberflächenfehler erhöht sich die Oberfläche und damit die Angriffsfläche für korrosive Einflüsse.
2. Falsche Werkzeugauswahl
Unter Umständen können die eingesetzten Werkzeuge für die Verarbeitung des Werkstoffes nicht geeignet sein. So kann zum Beispiel beim Schneiden eines Gewindes durch ein ungeeignetes Werkzeug das Gewinde nicht sauber und vollständig geschnitten werden, wodurch es bei der Montage zu Kaltverschweißungen kommen kann. Gleiches gilt auch für das Umformen von Gewinden. Auch hier kann durch falsche oder defekte Werkzeuge die vorgenannte Situation eintreten.
3. Härteunterschied
Einer der häufigsten Ursachen für das Festfressen ist die Unterschreitung einer Härtedifferenz zwischen Schrauben- und Mutterngewinde. Diese Differenz ist essentiell dafür verantwortlich, dass sich die Verbindungselemente nicht durch physikalisch-chemische Reaktionen dauerhaft verbinden ("festfressen"). Es sollte eine Härtedifferenz von mindestens 50 HV angestrebt werden um die Gefahr zu minimieren. In der Regel ist dies bei kaltumgeformten Verbindungselementen der gleichen Festigkeitsklasse sichergestellt, da das Schraubengewinde durch den Umformprozess eine deutliche Kaltverfestigung in den Gewindeflanken erfährt. Um die Gefahr beim Einsatz unterschiedlicher Werkstoffe zu reduzieren sollten vor der Herstellung die Lieferzustände (mechanische Eigenschaften) der Vormaterialien verglichen werden.
Eine zusätzliche Sicherheit kann durch den Einsatz entsprechender Gleitpasten erzielt werden, die vor der Montage auf das Schraubengewinde aufgebracht werden. Diese Maßnahme wird häufig bei so genannten Heißschraubenverbindungen angewandt, um das Verschweißen der Verbindungeelemente bei hohen Einsatztemperaturen zu verhindern.
Quelle:
Wilke, F. (2002) ThyssenKrupp Steel Kurzbericht 2806 - Wie vermeide ich das Festfressen rostfreier Verbidnungselemente?
Online: http://www.edelstahl-rostfrei.de/downloads/ISER/Festfressen_vermeiden.pdf (05.09.2011)
Duplex Stähle
Allgemeines
Als Duplex-Stahl werden Werkstoffe bezeichnet, die ein zweiphasiges Gefüge aufweisen (Ferrit und Austenit). Duplex-Stähle zeichnen sich durch ihre Kombination von Eigenschaften aus, die eine Mischung aus den Eigenschaften rostfreier Chromstähle (ferritisch oder martensitisch) und rostfreier Chrom-Nickel-Stähle (austenitisch) darstellen.
Sie haben höhere Festigkeiten als die rostfreien Chrom-Nickel-Stähle, weisen dabei aber eine höhere Duktilität auf als rostfreie Chromstähle. Ihr Verhalten bei wechselnder Beanspruchung weist bis zu einem Austenitanteil von ca. 40% im Gegensatz zu reinen Austeniten noch eine Dauerschwingfestigkeit auf. Die Duplex-Stähle zählen zu den rost- und säurebeständigen Stählen.
PREN-Index
Der PREN-Index ist ein Maß für die Korrosionsbeständigkeit eines Edelstahls. Die ASTM G48 legt die Prüfverfahren dazu fest.
Bei korrosionsbeständigen Stählen werden die für das Korrosionsverhalten entscheidenden chemischen Elemente durch die PREN, die einen Zusammenhang zwischen der Lochfraßbeständigkeit und der chemischen Zusammensetzung herstellt, zusammengefasst.
PREN = %Cr + 3,3 x %Mo (Ferritische Stähle)
PREN = %Cr + 3,3 x %Mo + 16 x %N (Austenitische Stähle)
PREN = %Cr + 3,3 x %Mo + 30 x %N (Duplex-Stähle)
Ferritisch-austenitische Duplex-Stähle mit PREN > 40 werden auch als Superduplex-Stähle bezeichnet und zeichnen sich durch eine besonders hohe Korrosionsbeständigkeit aus. Stähle mit PREN-Werten über 32 gelten als salzwasserbeständig.
Quellen:
DIN EN ISO 15156-3 - Erdöl- und Erdgasindustrie - Werkstoffe für den Einsatz in H2S-haltiger Umgebung bei der Öl- und Gasgewinnung - Teil 3: Hochlegierte Stähle (CRAs) und andere Legierungen
NACE MR0175/ISO 15156 - Petroleum and natural gas industries—Materials for use in H2S-containing environments in oil and gas production
ASTM G48 - Standard Test Methods for Pitting and Crevice Corrosion Resistance of Stainless Steels and Related Alloys by Use of Ferric Chloride Solution
Festigkeitsklassen
Die Festigkeitsklasse bei Schrauben besteht aus zwei Zahlen, die durch einen Punkt getrennt werden. Die Zahl links entspricht 1/100 der Nennzugfestigkeit Rm in MPa. Die Zahl rechts vom Punkt gibt das 10-fache des Verhältnisses zwischen Streckgrenze Re und Zugfestigkeit Rm (Streckgrenzenverhältnis). Daraus ergeben sich folgende Werte: 0,6 / 0,8 / 0,9. Diese Verhältniszahlen werden mit 10 multipliziert und ergeben dann den Wert nach dem Punkt.
Beispiel:
Eine Schraube mit der Zugfestigkeit Rm = 1.000 MPa und einem Streckgrenzenverhältnis von 0,9 hat somit die Festigkeitsklasse 10.9.
Formel zur Ermittlung der Festigkeitsklasse
Zugfestigkeit Rm: 1. Zahl X 100
Streckgrenze Re: (1. Zahl X 100) X (2.Zahl / 10)
Beispiel:
Schraube 10.9
Zugfestigkeit Rm: 10 x 100 = 1.000 MPa
Streckgrenze Re: (10 x 100) x (9 / 10) = 1.000 x 0,9 = 900 MPa
Übersicht alte und neue Festigkeitsklassen
Neue Bezeichnung | 3.6 | 4.6 | 4.8 | 5.6 | 5.8 | 6.6 | 6.8 | 6.9 | 8.8 | 10.9 | 12.9 |
Alte Bezeichnung | 4A | 4D | 4S | 5D | 5S | 6D | 6S | 6G | 8G | 10K | 12K |
Passende Mutter | 5 | 6 | 8 | 10 | 12 |
Quellen:
DIN 267-3 - Mechanische Verbindungselemente; Technische Lieferbedingungen; Festigkeitsklassen für Schrauben aus unlegierten oder legierten Stählen; Umstellung der Festigkeitsklassen
DIN EN ISO 898-1 - Mechanische Eigenschaften von Verbindungselementen aus Kohlenstoffstahl und legiertem Stahl - Teil 1: Schrauben mit festgelegten Festigkeitsklassen - Regelgewinde und Feingewinde
Schweissbarkeit von Stählen
Stähle mit einem Kohlenstoffgehalt von mehr als 0,22 % gelten nur noch als bedingt schweißbar, es sind zusätzliche Maßnahmen wie beispielsweise das Vorwärmen erforderlich. Der Kohlenstoffgehalt des Stahls alleine macht jedoch keine Aussage über die Schweißbarkeit, da diese auch von vielen anderen Legierungselementen beeinflusst wird. Zur Beurteilung wird daher das so genannte Kohlenstoffäquivalent (CEV) berücksichtigt.
Das Kohlenstoffäquivalent ist in der Werkstoffkunde ein Maß zur Beurteilung der Schweißeignung von unlegierten und niedriglegierten Stählen. Der Kohlenstoffgehalt und eine Vielzahl anderer Legierungselemente im Stahl beeinflussen sein Verhalten. Zur Beurteilung der Schweißeignung ist deshalb im Kohlenstoffäquivalent der Kohlenstoffgehalt und der gewichtete Anteil der Elemente, welche die Schweißeignung des Stahls ähnlich beeinflussen, wie es vom Kohlenstoff zu erwarten wäre, zu einem Zahlenwert zusammengefasst. Dabei impliziert ein Wert des Kohlenstoffäquivalents kleiner 0,45 % eine gute Schweißeignung. Höhere Werte erfordern - abhängig von der Verarbeitungsdicke - das Vorwärmen des Materials. Ab einem Wert größer 0,65 ist das Werkstück nur mit erhöhtem Aufwand schweißgeeignet, da es durch Martensitbildung zu Kalt- bzw. Härterissen kommen kann.
Ein gängiges Verfahren für die Berechnung des Kohlenstoffäquivalents (CEV) sieht folgendermaßen aus:
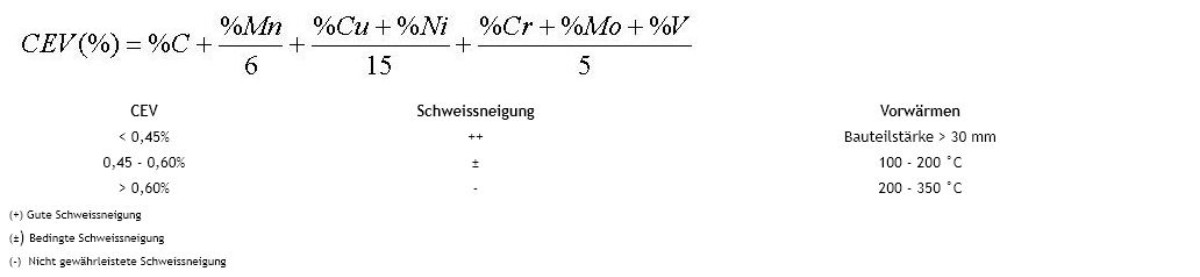
Die Legierungsanteile sind in Prozent einzusetzen. Häufig wird im Werkstoffzeugnis das Kohlenstoffäquivalent angegeben, sodass der Anwender diese Berechnung nicht selbst vornehmen muss. Unter Umständen ist jedoch die Nutzbarkeit des dort angegebenen CEV für die spezielle Anwendung zu hinterfragen.
Quelle:
Wittel, H. / Muhs, D. / Jannasch, D. / Voßiek, J. (2009) Roloff/Matek Maschinenelemente - Normung, Berechnung, Gestaltung; 19. Auflage; Vieweg+Teubner Verlag; Wiesbaden
ASTM - Werkstoffe
Kennzeichnung | Norm | Beschreibung | Material | Vergleichbarer EN Werkstoff |
---|---|---|---|---|
No Grade Mark |
SAE J429 Grade 1 |
Bolts, Screws, Studs |
Low or Medium Carbon Steel |
--- |
ASTM A307 Grade A & B |
Low Carbon Steel | --- | ||
SAE J429 Grade 2 |
Low or Medium Carbon Steel |
--- | ||
No Grade Mark | SAE J429 Grade 4 |
Studs | Medium Carbon Cold Drawn Steel |
--- |
B5 | ASTM A193 Grade B5 |
Bolts, Screws, Studs for high temperature service Class 1: Carbide solution treated |
AISI 501 | ~1.7362 |
B6 | ASTM A193 Grade B6 |
AISI 410 | ~1.4006 | |
B7 | ASTM A193 Grade B7 |
AISI 4140, 4142, 4105 | ~1.7225 | |
B16 | ASTM A193 Grade B16 |
CrMoVa Alloy Steel |
~1.7711 | |
B8 | ASTM A193 Grade B8 Class 1 |
AISI 304 | ~1.4301 | |
B8C | ASTM A193 Grade B8C Class 1 |
AISI 347 | ~1.4550 | |
B8M | ASTM A193 Grade B8M Class 1 |
AISI 316 | ~1.4401 | |
B8T | ASTM A193 Grade B8T Class 1 |
AISI 321 | ~1.4541 | |
B8 | ASTM A193 Grade B8 Class 2 |
Bolts, Screws, Studs for high temperature service Class 2: Carbide solution treated and strain hardened |
AISI 304 Strain Hardened |
~1.4301 |
B8C | ASTM A193 Grade B8C Class 2 |
AISI 347 Strain Hardened |
~1.4550 | |
B8M | ASTM A193 Grade B8M Class 2 |
AISI 316 Strain Hardened |
~1.4401 | |
B8T | ASTM A193 Grade B8T Class 2 |
AISI 321 Strain Hardened |
~1.4541 | |
L7 | ASTM A320 Grade L7 |
Bolts, Screws, Studs for low temperature service Quenched and tempered |
AISI 4140, 4142, 4145 |
~1.7225 |
L7A | ASTM A320 Grade L7A |
AISI 4037 | --- | |
L7B | ASTM A320 Grade L7B |
AISI 4137 | ~1.7220 | |
L7C | ASTM A320 Grade L7C |
AISI 8740 | ~1.6546 | |
L43 | ASTM A320 Grade L43 |
AISI 4340 | ~1.6580 | |
B8 | ASTM A320 Grade B8 Class 1 |
Bolts, Screws, Studs for low temperature service Class 1: Carbide solution treated |
AISI 304 | ~1.4301 |
B8C | ASTM A320 Grade B8C Class 1 |
AISI 347 | ~1.4550 | |
B8T | ASTM A320 Grade B8T Class 1 |
AISI 321 | ~1.4541 | |
B8F | ASTM A320 Grade B8F Class 1 |
AISI 303 (Se) | ~1.4305 | |
B8M | ASTM A320 Grade B8M Class 1 |
AISI 316 | ~1.4401 | |
B8 | ASTM A320 Grade B8 Class 2 |
Bolts, Screws, Studs for low temperature service Class 2: Carbide Solution treated and strain hardend |
AISI 304 | ~1.4301 |
B8C | ASTM A320 Grade B8C Class 2 |
AISI 347 | ~1.4550 | |
B8T | ASTM A320 Grade B8T Class 2 |
AISI 321 | ~1.4541 | |
B8F | ASTM A320 Grade B8F Class 2 |
AISI 303 (Se) | ~1.4305 | |
B8M | ASTM A320 Grade B8M Class 2 |
AISI 316 | ~1.4401 | |
3 Radial Lines 120° |
SAE J429 Grade 5 |
Bolts, Screws, Studs |
Medium Carbon Steel Quenched and Tempered |
--- |
ASTM A449 | --- | |||
3 Radial Lines 90° |
SAE J429 Grade 5.1 |
Bolts, Screws, Studs |
Low or Medium Carbon Steel Quenched and Tempered |
--- |
3 Radial Lines 60° | SAE J429 Grade 5.2 |
Bolts, Screws, Studs | Low Carbon Martensitic Steel Quenched and Tempered |
--- |
A325 | ASTM A325 Type 1 |
High strength structural bolts |
Medium Carbon Steel Quenched and Tempered |
--- |
--- | ASTM A325 Type 2 (Withdrawn) |
Low Carbon Martensitic Steel Quenched and Tempered |
--- |
|
A325 | ASTM A325 Type 3 |
Atmospheric Corrosion Resisting Steel Quenched and Tempered |
--- |
|
BD | ASTM A354 Grade BD |
Bolts, Studs |
Alloy Steel Quenched and Tempered |
--- |
BC | ASTM A354 Grade BC |
--- | ||
5 Radial Lines | SAE J429 Grade 7 |
Bolts, Screws | Medium Carbon Alloy Steel Quenched and Tempered |
--- |
6 Radial Lines 60° | SAE J429 Grade 8 |
Bolts, Screws, Studs | Medium Carbon Alloy Steel Quenched and Tempered |
--- |
No Grade Mark | SAE J429 Grade 8.1 |
Studs | Medium Carbon Alloy or SAE 1041 Modified Elevated Quenched and Tempered |
--- |
A490 | ASTM A490 | High strength structural bolts |
Alloy Steel Quenched and Tempered |
|
Quellen: http://praticalmaintenance.wordpress.com (24.08.2011) |
Sonderschrauben Güldner GmbH & Co. KG erhebt und verarbeitet die in dem Formular angegebenen personenbezogenen Daten, um für Sie die gewünschte Anfrage zu bearbeiten. Bitte beachten Sie bei den Formularen die Markierung der Pflichtfelder. Rechtsgrundlage für diese Verarbeitung, der zwingend erforderlichen Daten, ist Art. 6 Abs. 1 lit. b DSGVO, Durchführung einer vorvertraglichen Maßnahme. Die Verarbeitung der von Ihnen freiwillig mitgeteilten Daten erfolgt auf der Grundlage von Art. 6 Abs. 1 lit. f DSGVO. Danach ist eine Verarbeitung zulässig, die zur Wahrung der unserer berechtigten Interessen erforderlich ist. Unser berechtigtes Interesse besteht darin, mit Ihnen, unseren Kunden, Kontakt zu haben, unsere Beratungsqualität zu verbessern und Sie bei möglichen Rückfragen einfacher kontaktieren zu können. Die erhobenen Daten werden von uns nur solange gespeichert, wie es für die Bearbeitung Ihrer Anfrage sowie zur Kontaktaufnahme mit Ihnen erforderlich ist. Danach werden sie gelöscht.
Ergänzende Datenschutzhinweise, insbesondere zu Ihren Rechten auf Auskunft, Berichtigung, Löschung, Einschränkung der Verarbeitung, Widerspruch und Beschwerde, finden Sie in unserer Datenschutzerklärung.