Revêtement
Types de revêtements pour vis et attaches
Lorsqu'il s'agit d'assembler des pièces métalliques, les vis jouent un rôle crucial. Toutefois, pour garantir la durabilité et la fiabilité de ces assemblages, il est important de protéger les vis et autres fixations contre la corrosion et l'usure. C'est là que les revêtements entrent en jeu. Vous trouverez ci-dessous les revêtements les plus courants pour les vis et les types de revêtements pour les fixations que nous proposons.
Revêtement galvanique de vis et d'attaches spéciales
La galvanoplastie offre une protection optimale contre la corrosion et une durabilité accrue pour les vis et les attaches. Pour en savoir plus, cliquez ici.
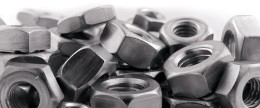
Le revêtement de zinc lamellaire offre une excellente protection contre la corrosion. Un mélange de paillettes de zinc et d'aluminium est appliqué sur la surface du métal sans utiliser de procédés électrolytiques.
Ce revêtement est particulièrement résistant aux influences chimiques et mécaniques.
Fréquemment utilisé sur des pièces soumises à de fortes contraintes, comme les vis et les pièces en acier, le revêtement de zinc lamellaire prolonge la durée de vie et les performances des pièces. Le processus est généralement réalisé par filage ou pulvérisation, suivi d'un traitement thermique qui forme une couche de protection uniforme.
Le revêtement de zinc lamellaire augmente considérablement la résistance à la corrosion du métal, ce qui protège les composants des influences environnementales et des contraintes mécaniques.
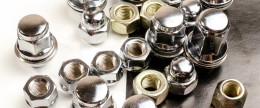
Le nickelage sert à la fois de décoration et de protection contre la corrosion. En raison de la dureté du revêtement, il convient à la construction d'équipements électriques et à l'industrie du téléphone. Il n'y a pas d'abrasion du revêtement, en particulier sur les vis. Les pièces en fer nickelé ne sont pas recommandées pour une utilisation à l'extérieur. L'imprégnation permet d'améliorer la protection contre la corrosion.
Le nickelage d'un métal est une méthode qui consiste à appliquer une fine couche de nickel sur la surface du métal. Ce procédé est souvent utilisé pour des raisons esthétiques, pour protéger le métal de la corrosion ou pour améliorer sa dureté et sa résistance à l'usure.
Il existe plusieurs méthodes de nickelage. Le nickelage électrolytique est une méthode courante. Dans ce procédé, le métal à nickeler est immergé dans un bain d'électrolyte en tant que cathode. Les ions de nickel sont dissous de l'anode par le courant électrique et se déposent sur la surface du métal. Il en résulte une couche uniforme de nickel sur le métal.
Le nickelage chimique est une autre approche. Le métal est immergé dans un mélange de composés de nickel. Le nickel est transféré de la solution à la surface du métal par des réactions chimiques. Cette méthode de nickelage est particulièrement adaptée aux pièces de forme complexe.
Le nickelage présente de nombreux avantages. Tout d'abord, le métal est protégé de la corrosion par la couche de nickel. Le nickel, métal extrêmement résistant, protège la surface du métal de l'humidité, des acides et d'autres substances nocives. En outre, le nickelage augmente la résistance à l'usure et la dureté du métal. Le nickel est un métal dur qui forme une couche solide sur la surface. Cela rend le métal plus résistant aux rayures, à l'abrasion et à d'autres contraintes mécaniques.
Le nickelage est également possible pour des raisons esthétiques. Le nickelage donne aux métaux un aspect brillant et argenté qui les met en valeur. Il est souvent utilisé sur les bijoux, les accessoires, les composants de véhicules et d'autres articles pour lesquels un aspect attrayant est important.
En résumé, le nickelage est une technique utilisée pour protéger le métal de la corrosion, améliorer sa dureté, sa résistance à l'usure et son apparence. Différents procédés peuvent être utilisés en fonction des exigences et des propriétés spécifiques du métal. Le nickelage est une technique bien établie qui est utilisée dans de nombreuses industries.
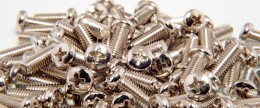
La veralisation est un procédé spécial de nickelage dur. Lors du processus de veralisation, une couche de nickel est appliquée à la surface d'un métal afin de le durcir et de le rendre résistant à l'usure. Il s'agit d'une forme particulière de nickelage dur dans laquelle une couche de nickel particulièrement épaisse est appliquée.
La veralisation est souvent utilisée pour les composants exposés à des charges élevées, tels que les outils, les pièces de machines ou les pièces d'usure. L'épaisse couche de nickel rend la surface du métal plus résistante à l'abrasion, aux rayures et à d'autres influences mécaniques. La durée de vie et les performances des composants s'en trouvent améliorées.
En règle générale, le nickelage est réalisé par nickelage électrolytique. Le métal est immergé dans un bain d'électrolyte en tant que cathode, tandis que le nickel sert d'anode. Les ions de nickel sont libérés de l'anode par le courant électrique et se déposent sur la surface du métal. Afin d'obtenir un revêtement de nickel épais et uniforme, ce processus est réalisé sur une période plus longue.
L'alcalinisation augmente la dureté et la résistance à l'usure du métal. L'épaisse couche de nickel rend la surface plus résistante aux contraintes mécaniques, ce qui prolonge la durée de vie des composants. Comme le nickel est un métal résistant et qu'il forme une couche protectrice à la surface, le processus d'aluminisation protège également contre la corrosion.
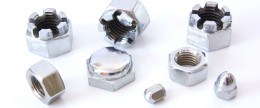
Le chromage est généralement appliqué après le nickelage. Une couche d'environ 4 µm de chrome a un effet décoratif, augmente la résistance au ternissement des pièces nickelées et améliore la protection contre la corrosion.
Le chromage des métaux est un procédé qui consiste à appliquer une fine couche de chrome sur la surface d'un métal. Ce procédé est souvent utilisé pour des raisons esthétiques ou pour protéger le métal de la corrosion et augmenter sa dureté.
Il existe plusieurs méthodes de chromage. Une méthode fréquemment utilisée est le chromage électrolytique. Dans ce procédé, le métal à chromer est immergé dans un bain d'électrolyte en tant que cathode. Le chrome est utilisé comme anode et les ions de chrome sont dissous à partir de l'anode et déposés sur la surface du métal par le flux du courant électrique. Cela forme une couche uniforme de chrome sur le métal.
Une autre méthode est le chromage chimique. Dans ce procédé, le métal est immergé dans une solution contenant des composés de chrome. Des réactions chimiques déposent le chrome de la solution sur la surface du métal. Cette méthode est souvent utilisée lorsque le métal a une forme complexe ou lorsqu'une épaisseur de couche uniforme est requise.
Le chromage présente plusieurs avantages. Tout d'abord, la couche de chrome protège le métal de la corrosion. Le chrome forme une couche protectrice à la surface qui protège le métal sous-jacent de l'humidité, des acides et d'autres influences néfastes.
En outre, le chromage augmente la dureté et la résistance à l'usure du métal. Le chrome est un métal dur qui forme une couche résistante à la surface. Cela rend le métal plus résistant aux rayures, à l'abrasion et à d'autres contraintes mécaniques.
Le chromage présente également des avantages esthétiques. Les revêtements chromés ont souvent un aspect brillant et réfléchissant qui rehausse l'apparence du métal. Ils sont souvent appliqués aux pièces de véhicules, aux accessoires, aux appareils ménagers et à d'autres produits pour lesquels un aspect attrayant est important.
- Chromé brillant: haute brillance
- Chromé mat: brillant mat (brillant satiné)
Le chromage des tambours n'est pas possible.
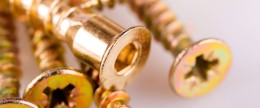
Les revêtements en laiton sont principalement utilisés à des fins décoratives. Les pièces en acier sont souvent revêtues de laiton afin d'améliorer la force d'adhérence du caoutchouc sur l'acier.
Le revêtement d'une surface métallique avec une fine couche de laiton est connu sous le nom de placage de laiton. L'alliage de laiton se compose principalement de cuivre et de zinc. Le placage de laiton est souvent utilisé pour protéger le métal de la corrosion, pour créer une surface décorative ou pour améliorer la conductivité électrique.
Il existe plusieurs techniques pour réussir le placage du laiton. Le placage électrolytique du laiton est une technique très répandue. Dans ce procédé, le métal utilisé pour le calibrage est immergé dans un bain d'électrolyte en tant que cathode. Une anode en laiton est également immergée dans le bain. Les ions de cuivre et de zinc sont dissous de l'anode par le courant électrique et se déposent sur la surface du métal. Cela crée une couche uniforme de laiton sur le métal.
Le laitonnage chimique est une autre méthode. Le métal est immergé dans une solution contenant des composés de cuivre et de zinc. Les ions de cuivre et de zinc sont déposés à partir de la solution sur la surface du métal par le biais de réactions chimiques. Ce procédé est souvent utilisé lorsque les vis ou les pièces ont des formes complexes et qu'une épaisseur de revêtement uniforme est requise.
Le placage de laiton présente de nombreux avantages. Le métal est protégé de la corrosion par le revêtement en laiton. Le laiton protège la surface de l'humidité, des acides et d'autres substances nocives.
La surface du métal est rehaussée par un placage en laiton. La couleur dorée et chaude du laiton n'est pas seulement esthétique, elle donne aussi au métal un aspect de haute qualité. C'est pourquoi il est souvent utilisé pour les bijoux, les accessoires, les objets décoratifs et d'autres articles pour lesquels un aspect attrayant est important.
En outre, le placage de laiton peut augmenter la conductivité électrique du métal. Le placage de laiton peut augmenter la conductivité d'un métal, ce qui peut être bénéfique dans certaines situations, car le laiton est un bon conducteur d'électricité.
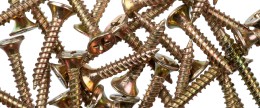
Le cuivrage est souvent utilisé comme couche intermédiaire avant le nickelage, le chromage et l'argenture. Il est utilisé comme couche supérieure à des fins décoratives.
Le cuivrage des vis et des attaches consiste à appliquer une fine couche de cuivre sur la surface du métal. Le cuivrage est souvent utilisé pour protéger le métal de la corrosion, pour créer une surface esthétique ou pour augmenter la conductivité électrique.
Il existe plusieurs techniques de cuivrage. Le cuivrage électrolytique est l'une des méthodes possibles. Dans cette méthode, le métal utilisé pour le cuivrage est immergé dans un bain d'électrolyte en tant que cathode. Une anode de cuivre est également immergée dans le bain. Les ions de cuivre sont dissous de l'anode par le courant électrique et déposés sur la surface du métal. Cela forme une couche uniforme de cuivre sur le métal.
Une autre méthode est le cuivrage chimique. Le métal est immergé dans une solution contenant des composés de cuivre. Des réactions chimiques déposent les ions de cuivre de la solution sur la surface du métal. Cette méthode est souvent utilisée lorsque le métal a une forme complexe ou lorsqu'une épaisseur de couche uniforme est requise.
Le cuivrage présente plusieurs avantages. Les vis ou autres attaches sont protégées de la corrosion par la couche de cuivre. Le cuivre forme une couche protectrice à la surface qui protège le métal sous-jacent de l'humidité, des acides et d'autres influences néfastes.
Le cuivrage confère également au métal une surface décorative. Le cuivre a une couleur chaude et rougeâtre qui est esthétique et donne au métal un aspect de haute qualité. Le cuivrage est souvent utilisé pour les bijoux, les accessoires, les objets décoratifs et d'autres produits pour lesquels un aspect attrayant est important.
En outre, le cuivrage peut contribuer à améliorer la conductivité électrique du métal. Le revêtement de cuivre peut être avantageux dans certaines situations, car il est un excellent conducteur électrique.
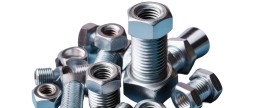
Les applications d'argent sont utilisées à des fins décoratives et techniques.
L'argenture des vis décrit l'application d'une couche d'argent à la surface des vis. Cette opération peut être effectuée pour des raisons esthétiques, afin de donner aux vis un aspect argenté, ou pour améliorer leur résistance à la corrosion.
Il existe plusieurs méthodes pour appliquer une couche d'argent sur les vis. Une méthode courante est l'argenture électrolytique. Les vis sont immergées dans une solution d'argent (cathode) et connectées à une source de courant continu. Le flux de courant électrique entraîne le dépôt de l'argent de la solution sur la surface des vis.
Une autre méthode est l'argenture chimique. Les vis sont immergées dans une solution contenant des ions d'argent. Une réaction chimique transfère l'argent de la solution à la surface des vis.
L'argenture des vis présente plusieurs avantages. Tout d'abord, il donne aux vis un aspect argenté esthétiquement agréable, ce qui peut être souhaitable dans certaines applications. Deuxièmement, le revêtement d'argent peut améliorer la résistance à la corrosion des vis, car l'argent est un métal noble et est moins sensible à la corrosion que d'autres métaux.
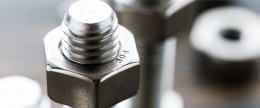
L'étamage est principalement utilisé pour obtenir ou améliorer la soudabilité (brasage tendre). Il sert également de protection contre la corrosion. Un post-traitement thermique n'est pas possible.
L'étamage des métaux est un processus qui consiste à appliquer une couche d'étain à la surface d'un métal. Cette opération peut être réalisée pour diverses raisons, telles que la protection contre la corrosion, l'amélioration de la soudabilité ou des raisons esthétiques. Le processus d'étamage comporte généralement plusieurs étapes :
1. Prétraitement: avant d'être étamé, le métal doit être soigneusement nettoyé pour éliminer les impuretés, les couches d'oxydation ou les pellicules de graisse. Cette opération peut être réalisée par différentes méthodes telles que le nettoyage chimique, le nettoyage mécanique ou le décapage.
2. Flux: Après le nettoyage, un flux est appliqué sur la surface du métal. Le flux aide à prévenir l'oxydation pendant le processus d'étamage et permet un meilleur mouillage du métal avec l'étain. Il existe différents types de flux, qui sont choisis en fonction de l'application et du type de métal.
3. Étamage: Après application du flux, le métal est immergé dans un bain d'étain ou recouvert d'une solution d'étain. Le bain d'étain est constitué d'étain fondu ou d'un alliage d'étain. Lorsque le métal est immergé, une couche d'étain se forme à la surface par diffusion ou par dépôt électrolytique.
4. Post-étamage: Après l'étamage, un post-traitement peut être nécessaire pour éliminer l'excès d'étain ou pour lisser la couche d'étain. Ce traitement peut être effectué par meulage, polissage ou d'autres procédés mécaniques ou chimiques.
Le processus d'étamage peut varier en fonction du type de métal, de la taille et de la forme de la pièce. Il nécessite généralement un équipement et une expertise spécialisés pour obtenir un résultat de haute qualité. L'étamage est utilisé dans diverses industries, telles que l'industrie électronique, la fabrication de récipients alimentaires ou la restauration d'objets métalliques historiques.
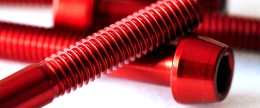
L'oxydation anodique crée une couche protectrice sur l'aluminium qui agit comme une protection contre la corrosion et empêche les taches. Pratiquement toutes les couleurs peuvent être obtenues à des fins décoratives.
L'anodisation des vis est un procédé de traitement de surface des métaux, en particulier de l'aluminium. Il s'agit d'un processus électrochimique dans lequel les vis sont traitées dans une solution électrolytique.
La principale raison de l'anodisation des vis est l'amélioration de la résistance à la corrosion. Le processus d'anodisation forme une fine couche d'oxyde dure et protectrice sur la surface des vis. Cette couche empêche la pénétration de l'humidité et d'autres substances nocives susceptibles de provoquer la corrosion. Cela permet de prolonger la durée de vie des vis et de préserver leur fonctionnalité.
En outre, l'anodisation offre également des avantages esthétiques. La couche d'oxyde peut être teintée en différentes couleurs, ce qui confère aux vis un aspect attrayant. Cet aspect est particulièrement important dans les endroits où les vis sont visibles, comme les meubles, les véhicules ou d'autres applications décoratives.
L'anodisation des vis permet également d'améliorer la résistance à l'usure. La couche d'oxyde est plus dure que le métal sous-jacent et offre donc une protection supplémentaire contre l'usure et les rayures.
En résumé, on peut dire que l'anodisation des vis est réalisée pour deux raisons principales : la protection contre la corrosion et l'amélioration des propriétés esthétiques. Il s'agit d'un procédé largement utilisé dans de nombreuses industries pour améliorer la durabilité et l'apparence des vis.
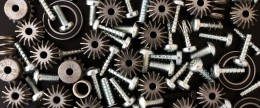
Immersion dans un bain de zinc à une température d'environ 440° - 470°C. Epaisseur du revêtement min. 40 µm. Surface mate et rugueuse, possibilité de coloration après un court laps de temps. Très bonne protection contre la corrosion.
Le traitement de surface des métaux, en particulier de l'acier, est réalisé par la galvanisation à chaud des pièces d'assemblage. Il s'agit d'un processus au cours duquel les pièces d'assemblage sont immergées dans du zinc liquide afin de créer une couche protectrice de zinc sur leur surface.
L'objectif principal de la galvanisation à chaud des pièces de fixation est de les protéger contre la corrosion. En les immergeant dans du zinc liquide, une couche de zinc se forme à la surface des pièces de liaison, ce qui empêche l'humidité et d'autres substances nocives de pénétrer. Cette couche de zinc offre une excellente protection contre la corrosion et prolonge considérablement la durée de vie des pièces d'assemblage, en particulier dans les environnements très humides ou dans des conditions chimiques agressives.
La galvanisation à chaud offre également une protection mécanique. Les pièces de raccordement sont protégées des rayures, de l'abrasion et d'autres contraintes mécaniques par la couche de zinc relativement dure et résistante. Ceci est particulièrement important pour les pièces de connexion qui sont exposées à des charges élevées, telles que celles utilisées dans la construction, l'industrie ou l'infrastructure.
La galvanisation à chaud présente également l'avantage d'être facile à appliquer. Comme plusieurs pièces d'assemblage peuvent être galvanisées en même temps, le processus est comparativement peu coûteux et efficace. En outre, le revêtement de zinc uniforme et sans joints constitue une couche de protection fiable.
La galvanisation à chaud des pièces d'assemblage est principalement utilisée pour la protection contre la corrosion et la protection mécanique. C'est un procédé éprouvé qui est utilisé dans de nombreux domaines pour améliorer la durabilité et la fiabilité des pièces de connexion, en particulier dans les applications extérieures ou dans les environnements agressifs.
- Acronyme: tZn
- Applicable aux pièces filetées à partir de M8
- La filetabilité peut être assurée par des mesures appropriées
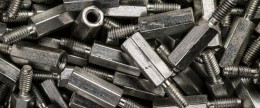
Excellent revêtement à base de zinc élevé (couleur gris argenté) pour les pièces présentant une résistance à la traction Rm ≥ 1 000 N/mm² (classes de résistance ≥10,9, dureté ≥ 300 HV). Avec ce procédé de revêtement, la fragilisation induite par l'hydrogène est exclue par la technologie du procédé.
Le revêtement d'un métal par une couche de zinc est appelé zingage inorganique. Il s'agit d'un processus électrochimique au cours duquel le métal est immergé dans une solution de zinc.
La protection contre la corrosion est l'objectif principal du revêtement de zinc inorganique. Le métal est protégé de l'humidité, de l'oxygène et d'autres substances corrosives par le revêtement de zinc. Le zinc est un anticorrosif qui se sacrifie au contact de l'humidité ou de l'oxygène pour protéger le métal sous-jacent. Ce processus est connu sous le nom de protection cathodique.
Le pouvoir adhésif élevé de la couche de zinc inorganique est un autre avantage. La couche de zinc adhère fermement à la surface du métal et forme un revêtement uniforme et sans interstices. Cela garantit une résistance élevée à l'abrasion, aux rayures et aux charges mécaniques.
Le revêtement de zinc inorganique offre également une grande résistance à la chaleur. En raison de son faible point de fusion, le revêtement reste stable à des températures élevées. Ceci est particulièrement important pour les applications où le métal est exposé à des températures élevées, comme dans l'industrie automobile ou chimique.
Une autre raison d'utiliser le revêtement de zinc inorganique est sa facilité d'application. Le processus est relativement peu coûteux et efficace, car plusieurs pièces métalliques peuvent être revêtues en même temps. En outre, la couche de zinc est mince et n'a aucun effet sur les dimensions ou le poids du métal.
- Résistant à la température jusqu'à environ 300 °C
- Applicable pour des filetages ≥ M4
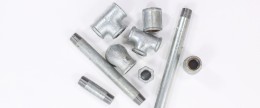
La galvanisation mécanique est un procédé de revêtement chimico-mécanique. Les pièces dégraissées sont placées dans un tambour de galvanisation avec un mélange spécial de billes de verre et de poudre de zinc. Les billes de verre servent de support aux grains de poudre de zinc et les amènent à la surface de la pièce, où ils se lient par soudage à froid.
La galvanisation mécanique des fixations métalliques est un procédé qui consiste à appliquer une couche de zinc sur la surface des boulons et des écrous. Par rapport à la galvanisation à chaud conventionnelle ou au revêtement de zinc inorganique, la galvanisation mécanique est un processus qui s'effectue sans l'utilisation d'électrolytes ou de solutions chimiques.
Lors de la galvanisation mécanique, les vis et les écrous sont placés dans un tambour ou un conteneur rempli de poudre de zinc et d'additifs spéciaux, tels que des billes de verre. En faisant tourner ou en secouant le tambour, les écrous et les boulons sont mis en contact avec la poudre de zinc. Le frottement mécanique entre les fixations et la poudre de zinc entraîne l'application du zinc sur la surface des écrous et des boulons.
Le principal objectif de la galvanisation mécanique des écrous et des boulons est la protection contre la corrosion. La couche de zinc appliquée forme une barrière protectrice entre le métal des fixations et l'environnement, empêchant ainsi la corrosion. La couche de zinc agit comme une protection sacrificielle contre la corrosion qui se sacrifie au contact de l'humidité ou de l'oxygène pour protéger le métal sous-jacent.
La galvanisation mécanique présente également l'avantage de répartir uniformément la couche de zinc sur les écrous et les boulons. En secouant ou en tournant le tambour, la poudre de zinc est appliquée uniformément sur la surface des fixations, ce qui permet d'obtenir un revêtement sans soudure.
La galvanisation mécanique des solutions de fixation présente également l'avantage de n'avoir aucun effet sur les dimensions ou le poids des fixations. La couche de zinc appliquée est fine et n'a aucun effet sur la fonctionnalité des fixations.
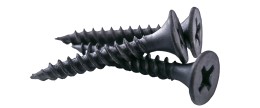
Le noircissement chimique est un procédé chimique permettant de noircir les aciers inoxydables à des fins décoratives.
Dans le processus de noircissement chimique de l'acier inoxydable, la surface du matériau est noircie par des réactions chimiques. Il s'agit d'un processus contrôlé au cours duquel la couche externe de l'acier inoxydable est transformée en une fine couche d'oxyde noir.
La formation de la couche d'oxyde noir donne à l'acier inoxydable une surface sombre, mate ou brillante, ce qui lui confère un aspect élégant et attrayant. Cet aspect peut être particulièrement important dans les applications décoratives ou dans la fabrication de bijoux, de montres, d'accessoires et d'autres produits.
En outre, le noircissement chimique présente également des avantages pratiques. La couche d'oxyde noir améliore la résistance de l'acier inoxydable à la corrosion et à l'usure. Elle forme une barrière protectrice contre l'humidité, l'oxygène et d'autres substances nocives qui pourraient attaquer le matériau. La couche d'oxyde peut également réduire la réflexion de la lumière et donc minimiser l'éblouissement.
Le noircissement chimique de l'acier inoxydable implique l'utilisation de solutions ou de bains chimiques spéciaux qui déclenchent les réactions souhaitées à la surface du matériau. La composition exacte des solutions peut varier en fonction des exigences spécifiques et de l'aspect souhaité. L'acier inoxydable est immergé dans le bain chimique ou la solution est appliquée à la surface pour déclencher la réaction et former la couche d'oxyde noir.
Il est important de noter que le noircissement chimique de l'acier inoxydable ne modifie pas de manière significative les propriétés du matériau. Les propriétés mécaniques et chimiques de l'acier inoxydable restent essentiellement inchangées, car la couche d'oxyde ne forme qu'une fine couche à la surface.
Le traitement de surface par noircissement chimique sert principalement à améliorer l'aspect esthétique de l'acier inoxydable et fournit également un certain degré de protection contre la corrosion.
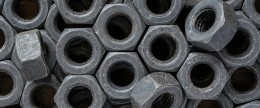
Le brunissage est un procédé chimique dans lequel on utilise un bain à une température d'environ 140 °C, suivi d'un huilage. Il convient bien à des fins décoratives et n'offre qu'une légère protection contre la corrosion.
Le brunissage est un procédé de traitement chimique de surface des métaux qui consiste à créer une fine couche d'oxyde de fer sur la surface du métal. Cette couche donne au métal une couleur sombre, noir-bleu, et fournit également un certain degré de protection contre la corrosion.
Le processus de brunissage se déroule en plusieurs étapes:
1. Nettoyage: La surface métallique est soigneusement nettoyée pour éliminer la saleté, la graisse et les autres contaminants. Il peut s'agir d'un nettoyage chimique, d'un dégraissage ou d'un nettoyage mécanique.
2. Activation: La surface métallique est activée pour faciliter la formation de la couche d'oxyde noir. Cela peut se faire par l'application d'un activateur ou par un prétraitement à l'acide.
3. Solution de brunissage: La surface métallique est immergée dans une solution de brunissage ou pulvérisée avec cette solution. La solution de brunissage contient généralement des sels tels que le nitrite de sodium ou le nitrate de potassium, qui réagissent avec la surface métallique et permettent la formation de la couche d'oxyde de fer.
4. Réaction: La solution de brunissage réagit avec la surface du métal et forme une fine couche d'oxyde de fer. Le temps de réaction peut varier en fonction de l'épaisseur de la couche et de la couleur souhaitées.
5. Neutralisation et rinçage: Après la réaction, la surface métallique est neutralisée pour arrêter la réaction chimique. La surface est ensuite soigneusement rincée à l'eau pour éliminer l'excès de solution de brunissage.
6. Préservation: Pour protéger la couche d'oxydation noire et améliorer la protection contre la corrosion, une couche de préservation peut être appliquée. Cela peut se faire en appliquant de l'huile ou de la cire, par exemple.
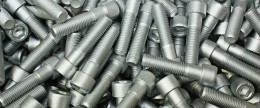
Ce revêtement n'offre qu'une légère protection contre la corrosion. Cependant, il offre un bon degré d'adhérence aux peintures. L'aspect est gris à gris-noir. Un huilage ultérieur améliore la protection contre la corrosion.
La phosphatation est un procédé de traitement de la surface des métaux qui consiste à former une couche de phosphate à la surface de la pièce. Pour ce faire, le métal est immergé dans une solution de phosphate ou une pâte de phosphate est appliquée.
Les vis de phosphatation sont souvent utilisées pour obtenir divers avantages:
1. Amélioration de l'adhérence: la couche de phosphate améliore l'adhérence des revêtements tels que le vernis, la peinture ou le revêtement en poudre à la surface de la vis. Il en résulte une meilleure résistance à l'usure.
2. Réduction du frottement: La couche de phosphate peut réduire la friction entre la vis et le matériau fixé. Cela facilite le vissage de la vis et réduit le risque d'endommagement ou de déformation de la vis par le matériau de fixation.
3. Une meilleure visibilité: La couche de phosphate peut réduire la friction entre la vis et le matériau de fixation. Cela facilite le vissage de la vis et réduit le risque d'endommagement ou de déformation de la vis par le matériau de fixation.
4. Protection contre la corrosion: La couche de phosphate forme une barrière protectrice sur la surface de la vis pour la protéger de la corrosion causée par l'humidité, l'oxygène et d'autres environnements corrosifs. L'huilage ultérieur des vis et des fixations renforce la protection contre la corrosion.
Dans l'ensemble, la phosphatation contribue à améliorer la durabilité, les performances et l'esthétique des vis, ce qui les rend adaptées à un large éventail d'applications.
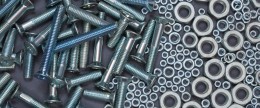
Dans le cas des éléments nickelés en particulier, le scellement des micropores avec de la cire peut être réalisé par un post-traitement avec un liquide d'égouttage contenant de la cire. La résistance à la corrosion s'en trouve considérablement améliorée. Le film de cire est sec et invisible.
Le traitement des fixations et des vis avec un fluide de déshydratation contenant de la cire est un processus visant à protéger les pièces concernées de la corrosion et à augmenter leur durée de vie.
Les fluides de déshydratation sont des solutions spéciales qui servent à éliminer l'eau de la surface des éléments. C'est très important, car l'eau est l'une des principales causes de la corrosion. En éliminant l'eau, le risque de corrosion est considérablement réduit.
L'additif de cire dans le fluide de déshydratation remplit plusieurs fonctions. La cire forme une couche protectrice à la surface des éléments, les protégeant de l'humidité et d'autres influences environnementales néfastes. Elle améliore les propriétés de frottement des pièces de raccordement, ce qui accroît leurs performances.
Le processus d'imprégnation avec un fluide de déshydratation contenant de la cire peut être réalisé comme suit:
1. Les éléments sont immergés dans le liquide de déshydratation.
2. Le fluide pénètre dans toutes les surfaces et fissures des éléments et déplace l'eau.
3. Les pièces de raccordement sont retirées du liquide et l'excédent de liquide est évacué.
4. Les pièces sont chauffées pour sécher le fluide et faire fondre la cire.
5. La cire fondue est étalée uniformément sur la surface des composants et forme une barrière protectrice.
6. Après refroidissement, les fixations sont imprégnées et prêtes à l'emploi.
Ce processus est réalisé dans un environnement contrôlé afin de s'assurer que les éléments sont imprégnés de manière uniforme et que l'imprégnation a les propriétés souhaitées.
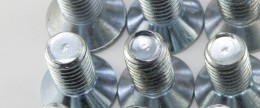
Les fixations électrodéposées en acier ayant une résistance à la traction Rm ≥ 1 000 N/mm² ou une dureté ≥ 320 HV qui sont soumises à une contrainte de traction risquent de se rompre en raison d'une fragilisation par l'hydrogène. Un revenu à environ 180°C à 230°C (en dessous de la température de revenu) peut partiellement éliminer l'hydrogène. Toutefois, selon l'état actuel de la technique, ce procédé n'offre pas une garantie à 100 %. Le recuit doit être effectué immédiatement après le traitement galvanique.
Le recuit est un processus de traitement thermique utilisé pour améliorer la dureté et la résistance de l'acier. Pour les fixations en acier qui ont été galvanisées, le recuit est une étape importante dans l'amélioration des propriétés mécaniques de l'acier et dans l'augmentation de la résistance à la corrosion du revêtement galvanique.
La galvanoplastie est un procédé qui consiste à appliquer une fine couche d'un métal sur la surface d'un autre métal afin d'en améliorer la résistance à la corrosion, l'aspect ou d'autres propriétés. Pour les fixations en acier, la galvanisation au zinc ou au nickel est souvent utilisée pour augmenter la résistance à la corrosion de l'acier.
Après la galvanisation, les fixations sont recuites pour améliorer leurs propriétés mécaniques. Le recuit consiste à chauffer l'acier à une certaine température, puis à le refroidir lentement. Ce processus modifie la structure microscopique de l'acier et entraîne une amélioration de sa dureté et de sa résistance.
En outre, le recuit peut contribuer à augmenter la résistance à la corrosion du revêtement galvanique. En chauffant puis en refroidissant, le revêtement peut être lié plus fermement à l'acier, ce qui le rend moins susceptible de s'écailler ou de s'endommager.
Le recuit doit être effectué avec soin pour garantir que les améliorations souhaitées sont obtenues sans endommager le revêtement galvanique. Cela nécessite un contrôle précis de la température et de la vitesse de refroidissement pendant le processus de recuit.
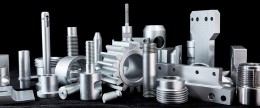
Le revêtement tribotechnique forme des couches qui réduisent le frottement et inhibent l'usure. Il offre une protection contre les frottements importants (grippage).
Les revêtements tribotechniques sont des revêtements spécialement conçus pour optimiser les propriétés tribologiques, c'est-à-dire le comportement des surfaces face au frottement et à l'usure. Ils sont souvent utilisés sur des pièces de machines exposées à des charges ou à des frottements élevés, comme les engrenages, les roulements, les pistons ou les vis.
Les revêtements peuvent être fabriqués à partir de divers matériaux, notamment des métaux, des céramiques, des polymères ou une combinaison de ces matériaux. Ils peuvent également contenir des additifs spécifiquement conçus pour réduire le frottement ou minimiser l'usure.
Les revêtements tribotechniques peuvent être appliqués de différentes manières, notamment par pulvérisation, trempage, galvanoplastie ou dépôt physique ou chimique en phase vapeur. Le processus exact dépend du type de revêtement et des exigences spécifiques de l'application.
Les avantages des revêtements tribotechniques sont nombreux. Ils peuvent contribuer à prolonger la durée de vie des pièces de machines, à augmenter leurs performances, à réduire les besoins de maintenance et à améliorer l'efficacité énergétique. En outre, ils peuvent contribuer à réduire l'impact environnemental des machines et des équipements en diminuant la consommation d'énergie et en réduisant les besoins en lubrifiants.
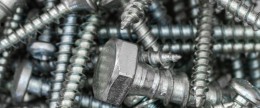
La cire crée une couche de glissement qui permet de réduire le couple d'insertion des vis taraudeuses.
Le "cirage" est un revêtement spécial qui est appliqué sur les vis à roulement à billes. Ce revêtement forme une "couche de glissement".
La couche de glissement a la propriété de réduire la friction entre la vis et le matériau dans lequel elle est vissée. Il en résulte une réduction du couple d'insertion, c'est-à-dire de la force nécessaire pour visser la vis dans le matériau.
Ce processus est particulièrement utile avec les vis à filetage, car ces vis ont tendance à avoir un couple d'insertion plus élevé en raison de leur conception. Elles forment leur propre filetage lorsqu'elles sont vissées dans le matériau, ce qui crée une friction supplémentaire. L'application d'une couche lubrifiante permet de réduire ce frottement supplémentaire et de faciliter le vissage de la vis.
Outre la réduction du couple d'insertion, la couche de glissement peut également contribuer à minimiser l'usure de la vis et à prolonger sa durée de vie. L'efficacité du revêtement antifriction dépend de plusieurs facteurs, notamment du type de revêtement, du type de matériau dans lequel la vis est vissée et de l'application spécifique de la vis.
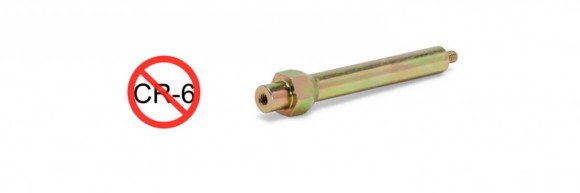
Interdiction des revêtements contenant du chrome (VI)
Depuis le 21 septembre 2017, il est interdit d’utiliser ou de mettre sur le marché les produits chimiques contenant du chrome (VI). Pour garder la possibilité d’une poursuite continuelle de l’utilisation dans le cadre de la règlementation REACH, une autorisation a dû être demandée avant le 21 mars 2016. Comme des preuves et études très dispendieuses sont requises pour obtenir une autorisation, on peut s’attendre à ce que les entreprises de galvanisation qui proposeront encore des revêtements contenant du chrome (VI) (p. ex. « galvanisé jaune ») à partir de l’année 2017.
Les revêtements suivants sont concernés:
- Galvanisé avec chromatage jaune (p. ex. A2C)
- Galvanisé avec chromatage olive
- Galvanisé avec chromatage noir
- Revêtement de zinc lamellaire contenant du chrome 6 (p. ex. Dacromet®)
Dans ce contexte, nous aimerions vous présenter ici des alternatives (sans chrome 6!):
Système | Sans chrome (IV) | Rouille blanche (h) | Rouille rouge (h) | Norme | Remarque | |||
Revêtement | Post-traitement | 5 µm | 8 µm | 12 µm | ||||
Zinc (Zn) | Chromé bleu | ✓ | 12 | 36 | 72 | 96 | EN ISO 4042 | ex. A2K, A3K |
Zinc (Zn) | Chromé jaune | X | 48 | 72 | 120 | 144 | EN ISO 4042 | ex. A2L, A3L |
Zinc (Zn) | Chromé olive | X | 72 | 96 | 144 | 168 | EN ISO 4042 | ex. A2D |
Zinc (Zn) | Chromé noir | X | 12 | - | 72 | 96 | EN ISO 4042 | ex. A2R |
Zinc (Zn) | Transparent passivé | ✓ | 8 | 48 | 72 | 96 | DIN 50979 | “Passivation en couche mince” |
Zinc (Zn) | Irisé passivé | ✓ | 72 | 144 | 216 | 288 | DIN 50979 | “Passivation en couche épaisse” |
Zinc (Zn) | Iridescent passivé + scellé | ✓ | 120 | 192 | 264 | 360 | DIN 50979 | |
Zinc-Fer (ZnFe) | Irisé passivé | ✓ | 96 | 168 | 240 | 312 | DIN 50979 | |
Zinc-Fer (ZnFe) | Iridescent passivé + scellé | ✓ | 144 | 216 | 288 | 384 | DIN 50979 | |
Zinc-Fer (ZnFe) | Noir passivé + scellé | ✓ | 120 | 192 | 264 | 360 | DIN 50979 | |
ZincNickel (ZnNi) | Irisé passivé | ✓ | 120 | 480 | 720 | 720 | DIN 50979 | |
ZincNickel (ZnNi) | Iridescent passivé + scellé | ✓ | 168 | 600 | 720 | 720 | DIN 50979 | |
ZincNickel (ZnNi) | Noir passivé + scellé | ✓ | 168 | 480 | 720 | 720 | DIN 50979 | |
Zinc lamellaire | Dacromet 320 ® | X | 250 | 600 | 1.000 | - | ISO 10683 | |
Zinc lamellaire | Geomet 321 ® | ✓ | 250 | 600 | 1.000 | - | ISO 10683 | |
Remarque: Si la dureté du composant dépasse 320 HV ou si la résistance à la traction Rm dépasse 1 000 MPa, le processus de fabrication doit être vérifié à l'aide d'un test de détection de la fragilisation par l'hydrogène. Dans ce cas, le revêtement galvanique doit généralement être évité afin d'exclure le risque de fracture due à la fragilisation par l'hydrogène. Un revêtement de zinc lamellaire peut être une alternative dans ces cas. Toutes les informations sont données sans garantie. |
Sonderschrauben Güldner GmbH & Co. KG recueille et traite les données personnelles saisies dans le formulaire afin de répondre à votre demande. Veuillez noter que les champs obligatoires sont marqués sur les formulaires. La base juridique de ce traitement des données obligatoires est l'art. 6 para. 1 lit. b GDPR, mise en œuvre d'une mesure précontractuelle. Le traitement des données que vous avez volontairement fournies est effectué sur la base de l'art. 6 para. 1 lit. f GDPR. Cette disposition autorise le traitement nécessaire à la sauvegarde de nos intérêts légitimes. Notre intérêt légitime est d'être en contact avec vous, nos clients, afin d'améliorer la qualité de nos conseils et de pouvoir vous contacter plus facilement en cas de questions. Les données collectées ne seront stockées par nous que le temps nécessaire pour traiter votre demande et vous contacter. Elles seront ensuite supprimées.
Des informations supplémentaires sur la protection des données, en particulier sur vos droits à l'information, à la rectification, à l'effacement, à la limitation du traitement, à l'objection et à la plainte, sont disponibles dans notre politique de protection de la vie privée.